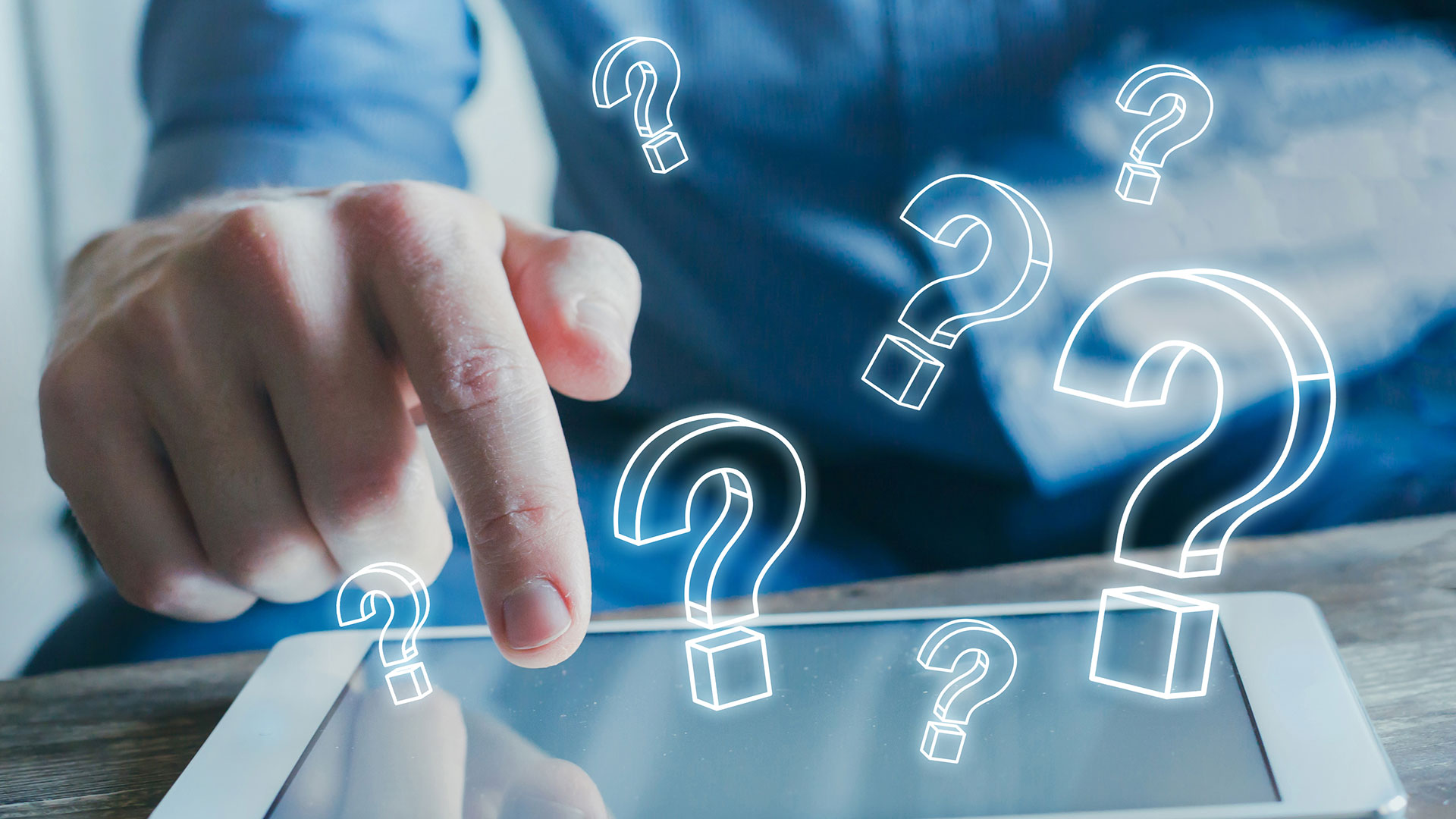
FAQs
Learn a little bit more about 3D printing, and ExOne.
Read our FAQs section below.
General Inquiries
How does ExOne® binder jet process work?
Based on the patented 3DP process developed at MIT, ExOne builds functional 3D objects from the bottom up, one layer at a time with durable, industrial-strength materials. See the Technology Overview page to find out about the process.
How durable are 3D printed components?
It depends on the material system used. For stainless steel and bronze metal parts, ultimate tensile strengths range between 60 and 100 ksi, with hardness levels of 20-30 HRc.
What is the surface quality?
The surface quality depends on your material choice. Each material has a different natural surface quality. This is also true for the various finishing options. For metal printing, we offer a variety of plating choices. Check out our materials pages for more specifics.
What kind of tolerances can you meet?
ExOne® sand printers can achieve printing tolerances of +/- 0.5 mm (0.02 in). ExOne® metal printers can achieve accuracies of +/- 0.13 mm (0.005 in) in components under 75 x 75 x 75 mm (3 x 3 x 3 in); +/- 0.25 mm (0.010 in) in components up to 250 x 250 x 250 mm (10 x 10 x 10 in); and +/- 1.3 mm (0.050 in) for the largest components up to 780 x 400 x 400 mm (30.7 x 15.75 x 15.75 in).
Can more than one part be printed simultaneously?
Yes. The software will allow for as many parts as can fit within the build box, and each can be different or fully customized. This maximizes time and minimizes waste. It takes as long to print one part as it does to print multiple parts in the build box.
Are other materials available?
Yes. Several metal options are currently in development. Please inquire about your specific needs and ExOne will determine feasibility.
Do you ship worldwide?
Yes. ExOne operates facilities on three continents and ships worldwide.
How do I get a price quote?
Contact one of our Global Facilities or Request a Quote online with your requirements.
Can I order from any of your facilities?
Yes. Each of our global facilities has the resources to take your order and forward it to the appropriate location for processing.
Sand Parts on Demand
What are the benefits of binder jet 3D printing for sandcasting?
Molds and cores printed with ExOne binder jet technology enable faster delivery times, new design freedoms, and reduced costs by utilizing a digital, pattern-less workflow. OEMs and foundries are optimizing their production with binder jetting to deliver castings with complex rigging designs and monolithic cores in days, rather than weeks or months, while saving money on patterns, molds, and labor.
How do I know if 3D printed sand molds or cores will meet my needs?
ExOne offers Parts on Demand using either metal or sand binder jet printing systems, but our team of metalcasting experts also offer a detailed analysis of your application's requirements. We carry out virtual casting with solidification modeling to determine the successfulness of a pour, create unique rigging and riser designs to maximize the benefits of additive manufacturing, and, of course, offer 3D printing of cores, complex prototype molds, or production-scale casting molds.
Is assistance available to create a digital file?
ExOne accepts a wide range of digital modeling file types, though STL is most preferred. If you need assistance creating a file that is suitable for 3D printed molds, please contact us for support.
What materials/binder can I print with?
ExOne machines print a variety of silica and ceramic sand materials. These pair with our variety of binder systems, including inorganic binders, to tailor a print to the requirements of the casting. Reach out to our team to learn about the material options and which combination is right for your needs.
When will my parts be available?
We have on-demand sand printing facilities located in the North America, Europe, and Asia. Standard lead time for 3D printed sand molds and cores varies by location and may depend on the complexity of the casting mold or volume of the order. In the Americas our turnaround times are as fast as 3-5 days. Rush services are available, so reach out to get a custom quote for 3D printing.
Can you accommodate the volume of my order?
The binder jetting process for 3D printing sand casting molds suits applications with a lot of 1 or 1,000,000. At ExOne, we’re equipped to help you quickly develop a casting mold for a one-off prototype and its ensuing iterations, as well as produce 3D printed molds and cores at scale. We also have a network of customers who offer sand printing services we can connect you with to make sure you find the perfect fit for your production needs.
I have a high-value, complex casting. Can you help me ensure a successful first pour?
Our team has a unique combination of metalcasting and binder jetting experience to enable easy design changes, quick turnarounds, and successful first pours. Our OneCast range of services include a requirement analysis, rigging and riser design, fluid flow and solidification modeling, creating detailed pouring parameters, mold assembly instructions, and on-site pour supervision. OneCast saves customers time and money efficiently delivering complex castings right the first time.
Can sand binder jet 3D printing be used to create tooling?
Yes - ExOne binder jet machines create pre-forms for a range of tooling applications. Sacrifical tooling can be printed in unique shapes and used for composite layup where the sand is simply washed out after autoclaving. Additionally, the patented AMClad® process inflitrates and coats sand prints to create large tools able of withstanding various types of molding and forming processes, such as vacuum and hydroforming or sheet metal stamping.
Washout Tooling on Demand
What is Washout Tooling commonly used for?
3D printed soluble support materials are designed to create hollow tooling and composite parts with trapped geometries. You can order parts on demand developed with washout tooling for aircraft ducting, pressure tanks, mandrels and more.
Can you help design a digital file?
ExOne accepts a wide range of digital modeling file types, though STL is most preferred, and files can be easily uploaded via our Request a Quote form. If you need assistance creating a file that is suitable for 3D printing, please inquire about our design services.
What is the typical coating applied to seal the core from resin infiltration?
Teflon® tape wrap or soluble spray-on coating. We can apply whatever coat you need to prepare the cores for finishing in your facility.
What composite materials are compatible?
Currently, ExOne only offers printed and coated cores. Composite layup, curing and washout is completed by our customers using filament winding or application of prepreg woven fabric. Common layup materials that can be applied to our cores are: carbon fiber, fiberglass, aramid fiber or ceramic matrix composites (CMC).
What is the maximum cure temperature for composite part manufacturing?
350°F (177°C)
Are ExOne 3D printed cores autoclave approved?
Yes. The core can withstand a maximum autoclave pressure of 85 psi during composite part production.
What do you use to washout the core after the composite part is produced?
Our cores are made with water-soluble support material and are able to be removed with room temperature tap water.
Are there any chemicals or toxins present during washout?
No.
When will I receive my 3D printed tooling?
Standard lead time for washout tooling is 7-10 working days to account for printing, curing and coating the cores. Additional production to apply the composite layup, cure the tooling and washout the core will be required after you receive the parts. Rush services are available.
Can you accommodate the volume of my order?
The binder jetting process is the most economical choice for 3D printing hollow objects. And lots of 1 can be just as efficient as lots of 1,000. Additionally, iterative or individually customized washout tooling can be printed in a single print run.
Metal Parts on Demand
What are the benefits of binder jet 3D printing for metal production?
ExOne’s patented binder jetting technology for metal offers many benefits over traditional manufacturing, other forms of 3D printing and other binder jet offerings in the marketplace. Among them:
- Faster time to market. Go immediately from design file to production.
- Flexibility. 3D print a variety of metal powders on the same machine, and only print what you need. Smaller batches are affordable with a metal 3D printer.
- Waste reduction. Binder jet 3D printing offers a dramatic waste reduction over traditional manufacturing methods, and eliminates the support structures and build plates necessary with other forms of metal 3D printing.
- Rapid design changes. Modifying designs and iterating for performance improvements is easy and affordable with binder jet 3D printing.
- Exceptional design freedom. With the new design possibilities offered by binder jet 3D printing, you can consolidate parts, eliminate manufacturing processes, reduce weight and save energy. What’s more, 3D printing offers a new approach to solving new or nagging problems.
How do I know I need a printed metal part?
ExOne offers on-demand 3D printing for metal parts as well as sand castings and specialty materials. The most common application of our 3D metal printing is the manufacture of customized, complex parts. We can handle a variety of throughput requests from rapid product development to serial production, and have finishing options that will help you efficiently bring your part from conception to market. Our customers also leverage our 3D metal printing service to create prototypes or conceptual models.
Will I require finishing services when 3D printing metal parts?
ExOne® metal Parts on Demand are “near-net,” meaning some finishing may be desired or required. We offer a full array of finishing services that can be added to our on-demand metal 3D printing packages. Please contact us for details.
Will I need assistance with creating a digital file?
ExOne accepts a wide range of digital modeling file types, though STL is most preferred, and files can be easily uploaded via our Request a Quote form. If you need assistance creating a file, please inquire about our design services for 3D metal printing.
When will my parts be available?
Standard lead time for 3D printing metal parts is 10 working days, but will depend on the volume and complexity of the job. Rush services are available, so reach out to get a customized quote for 3D metal print service.
Can you accommodate the volume of my order?
Iterative or individually customized parts can be managed in a single print run, but 3D metal printing services are also available for serial production. Whether manufacturing lots of 1 or 1,000, the binder jetting process is the most economical choice for 3D printing metal Parts on Demand.
How do I access the manufacturing guidelines for metal sintered parts?
Click here to download the manufacturing design guidelines.
How do I access the manufacturing guidelines for metal infiltrated parts?
Click here to download the manufacturing guidelines.