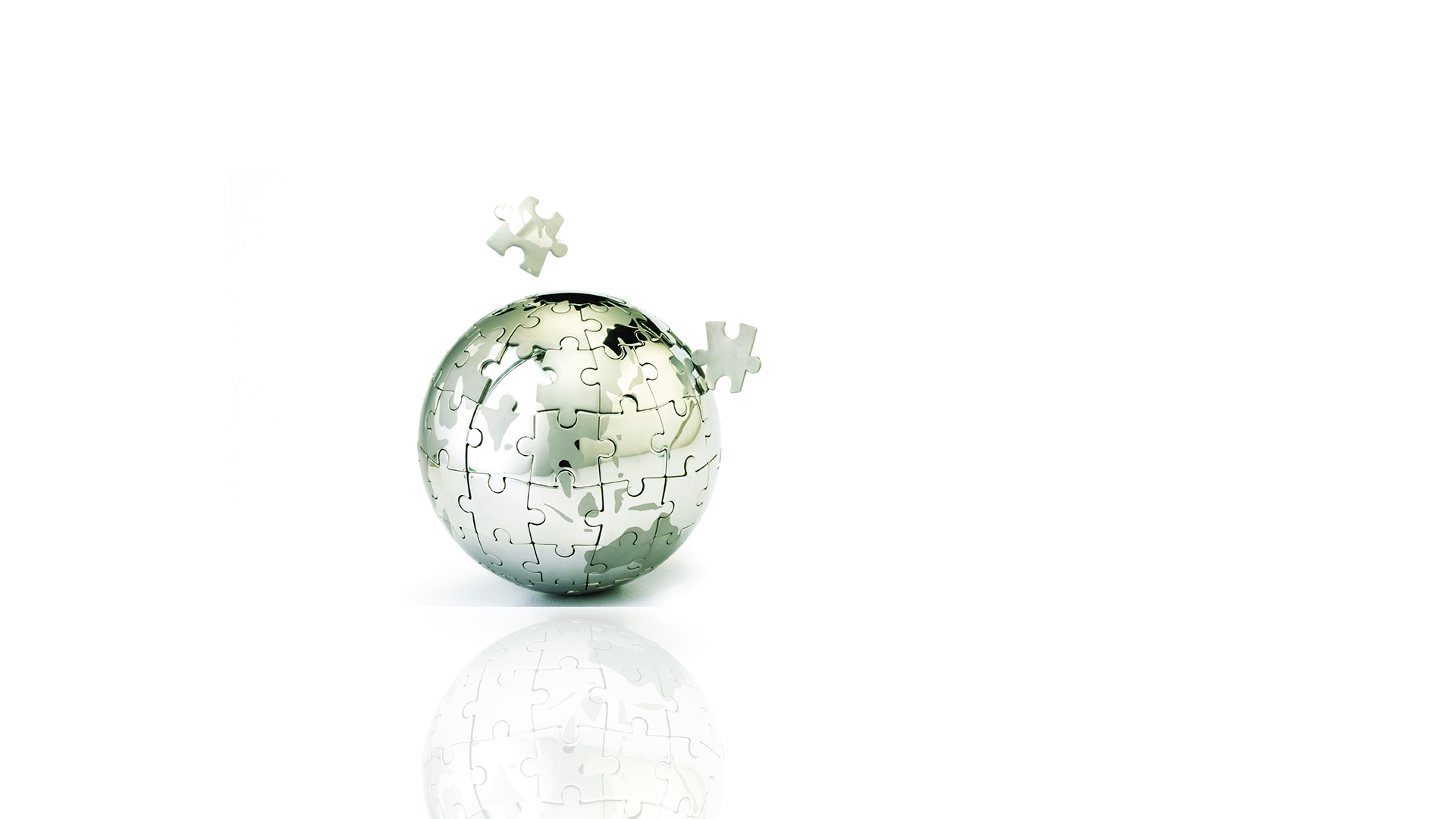
At ExOne, We've Always Been Green
From our inception as the 3D printing division of Extrude Hone in 1995, ExOne has always been focused on the sustainability benefits that binder jetting delivers.
We might not have used the popular sustainability buzzword back then, but reducing the waste associated with traditional manufacturing processes and improving design freedom has driven us from the beginning.