- Home
- Binder Jetting Resources
- Blog
3D Printing Attracts a New Generation of Workers
Embracing the Future Foundry Workforce
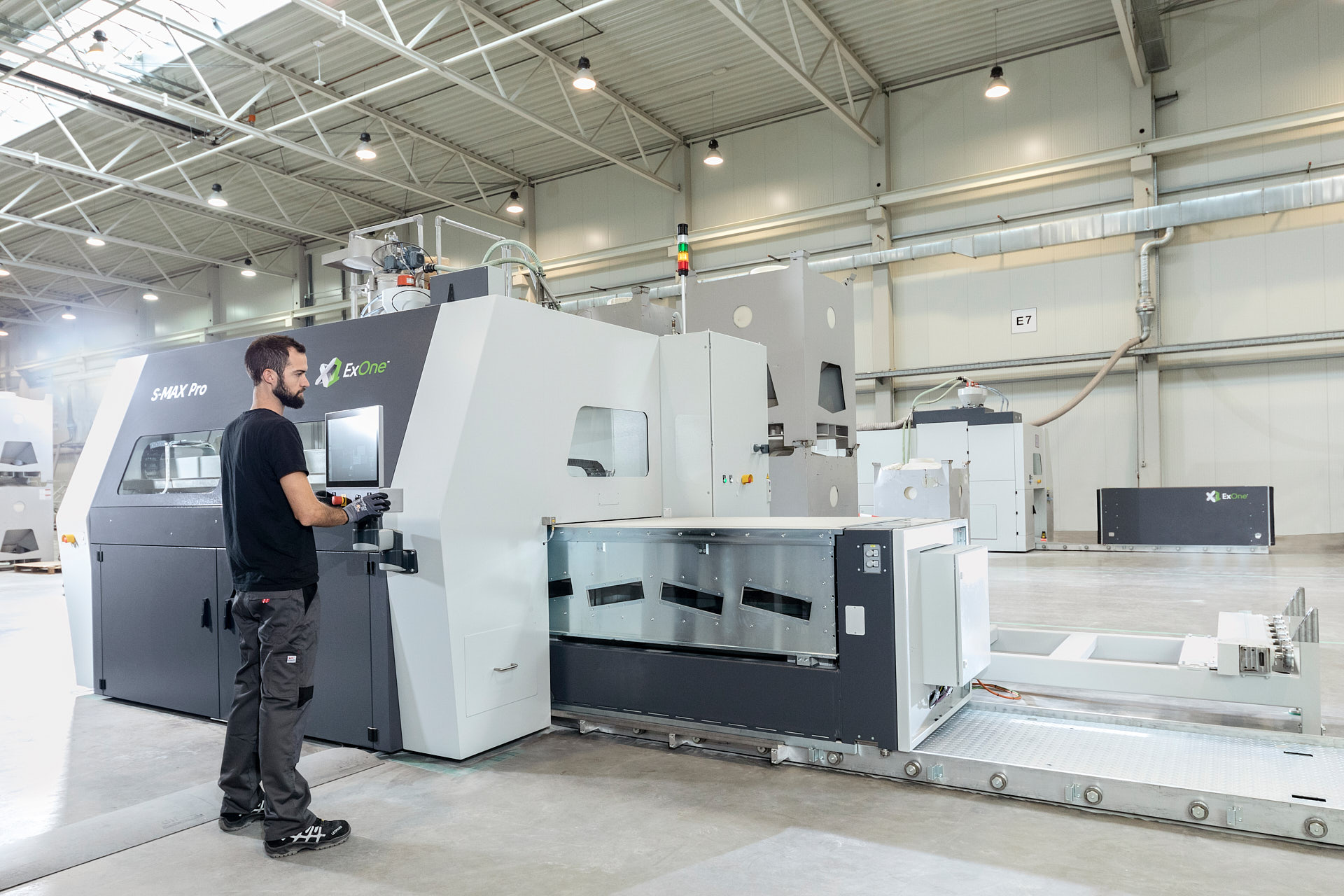
Embracing the Future Foundry Workforce
3D Printing Revolutionizes Sandcasting and Attracts a New Generation of Workers to the Foundry
The fourth industrial revolution is converging digital and physical processes and the manufacturing sector is continuing through a profound transformation thanks to the integration of cutting-edge technologies like 3D printing. Additive manufacturing not only enhances the efficiency and precision of production, it can also play a pivotal role in attracting a new generation of talent to the foundry.
According to a study by the Manufacturing Institute (MI), the industry faces a projection of 2.1 million unfulfilled jobs by 2030, “if we do not inspire more people to pursue modern manufacturing careers.” And especially in the foundry industry, where skilled workers are retiring every day, lack of knowledge and talent can prevent growth. Adopting technologies like 3D printing can help companies bridge the generational gap to millennial and, increasingly, Gen Z employees, making them stand out to attract workforce talent while also ensuring the future of their business to grow and take on new work.
Staying ahead of the curve:
A significant factor in attracting new workers to the foundry is the promise of a tech-savvy work environment. A generation that has grown up surrounded by digital tools expects to work in a high-tech setting – a idea that often clashes with the many misconceptions about metalcasting. They reject the notion of outdated production lines and prefer state-of-the-art facilities equipped with interconnectivity, 3D printing, robotics, and automation.
Furthermore, young professionals are eager to acquire new skills and stay relevant in an ever-evolving job market. 3D printing presents an exciting learning opportunity for workers to gain experience with an advanced technology and establish themselves as experts in the expanding additive field. With investments in technologies like binder jet 3D printing, foundries are increasingly a hub for continuous learning and professional development, appealing to a generation that values lifelong learning.
“Patternmaking is a dying trade. It’s not a skill that’s really taught anymore and technology is giving us new options.”
Austin Crawley, Program Manager, Dundee Castings
“We want to improve the work environment for the people that are making the product and these kinds of advanced manufacturing jobs are more attractive and help us retain people.”
Tyler Hill, Plant Manager, Grede Iron Mountain
Unleashing creative problem solving:
When looking where to start their careers, younger workers tend to focus on industries that foster innovation and creativity. With the expansion of consumer printers and maker spaces around the world, digital natives like Generation Z have not only grown up with the internet, but are increasingly native to once-obscure technologies like 3D printing. Younger generations, without the “experience” of traditional manufacturability constraints, are attracted to technologies that unleash creativity with the ability to turn digital concepts into tangible castings in a short amount of time.
Binder jetting also enables the manufacturing of highly-customized or improved-performance products, especially in driving new technologies like electrification, lightweighting, or other sustainability intiatives. Younger workers, accustomed to both fast results and personalized experiences in various aspects of their lives, are drawn to industries that offer opportunities to create unique products with quick turnarounds.
Metalcasting facilities that foster a dynamic and forward-thinking environment, and invest in the tools to bring ideas to life, are particularly attractive to younger generations who thrive on innovation and creative problem-solving.
“The changes that we need to make to a design we can do on the fly and provide a new sample within a day instead of weeks.”
Nick Bonikowske, Sample and Process Analyst, Waupaca Foundry
“We’ve reached a point now where our team is very young, intelligent, and forward thinking; our equipment and processes are state-of-the-art. Installing an ExOne S-Max is a major milestone in our company’s innovative vision.
Greg Witmyer, President, Kore Mart
Embracing environmental responsibility:
Younger workers, more than past generations, are interested in aligning their core values to their work. With increasing concern about the environmental impact of industries, foundries are looking at 3D printing technologies to help them operate more sustainably than with traditional manufacturing methods. ExOne binder jetting enables workers to produce complex parts that can both decrease foundry scrap rates and increase functional performance of the casting.
Binder jetting offers foundries an opportunity to work with inorganic binder systems that decrease emissions, reduce scrap waste, and operate with a more sustainable strategy to attract workers that value sustainability and corporate social responsibility.
“The post-processing of the cast part also requires much less time and effort because the printed impeller core does not have any drafts, the amount of post-processing is reduced.”
Torbjörn Andersson, 3D Technician, Xylem Water Solutions Manufacturing AB
“Sustainability is a big issue for us. We use 95% of the regenerates from the 3D printer.”
Dieter Diebold, Foundry Manager, Mezger AG
As the metalcasting sector continues to evolve, embracing 3D printing is not just a technological upgrade, it's also a strategic business move to attract new foundry workers. The fusion of innovation, growth, and sustainability makes sand 3D printing a key technology to help position foundries as exciting and dynamic for workforce of the future. Additive technologies like binder jetting can help foundries bridge the generational gap to propel the industry into a new era of success.
Advanced equipment also helps foundries operate more efficiently to help reduce the need for unfilled positions caused by a labor shortage. Binder jet sand 3D printers operate lights-out to produce complex molds and cores around the clock with less intervention and manual assembly required.
How Can Sand 3D Printing Help Your Foundry?
Learn more about binder jetting technology and see our range of solutions to help drive efficiency and growth into the future
DOWNLOAD OUR SOLUTIONS CATALOG