Morel Industries
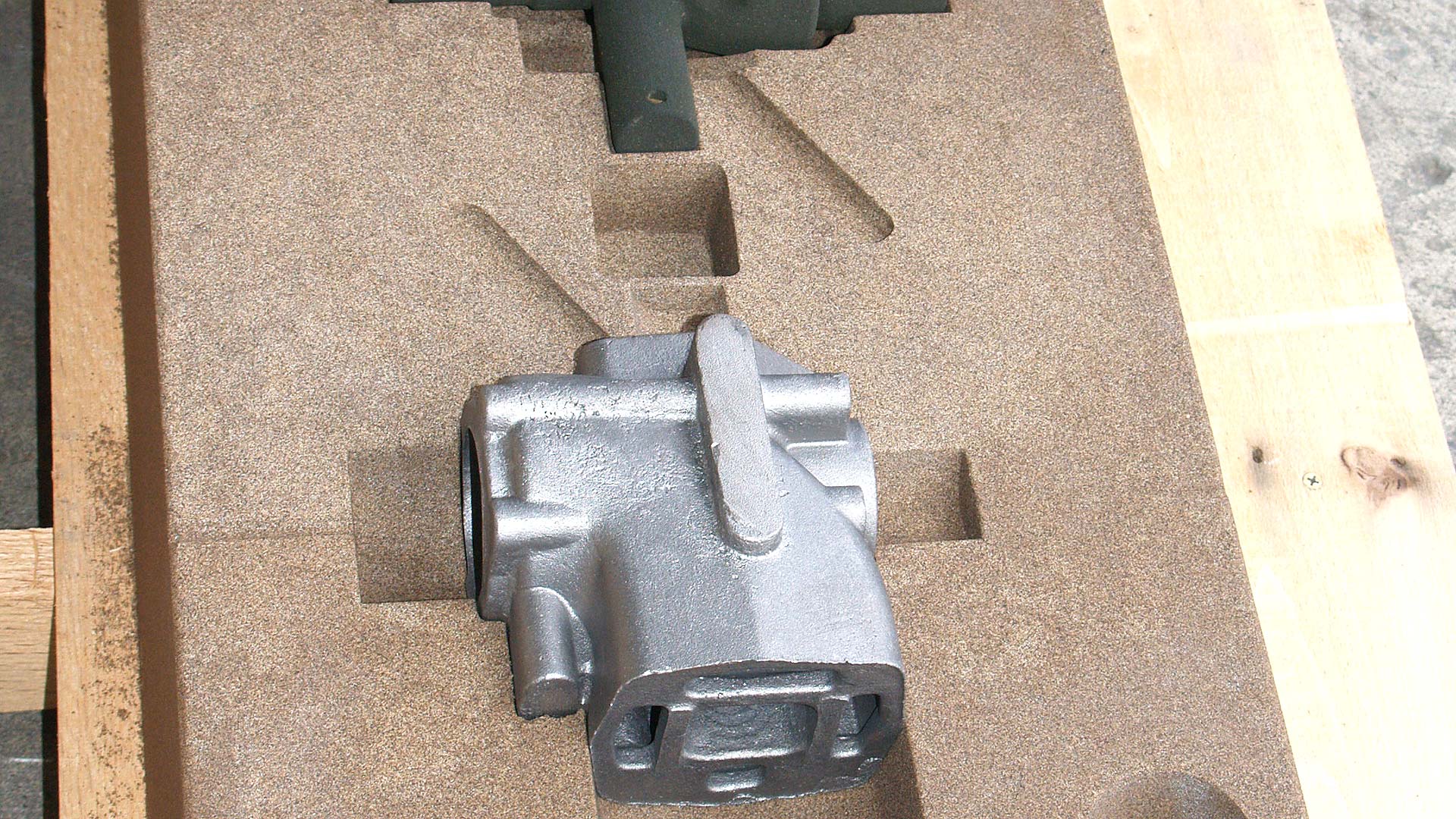
Morel Industries
Developing solutions to eliminate the human error in the assembly of core boxes used with traditional wood and sand patterns.
Documentation
Download Morel Industries
Complex Digital Core Cuts Lead Time in Half & Saves Thousands