The Evolution of the Revolution
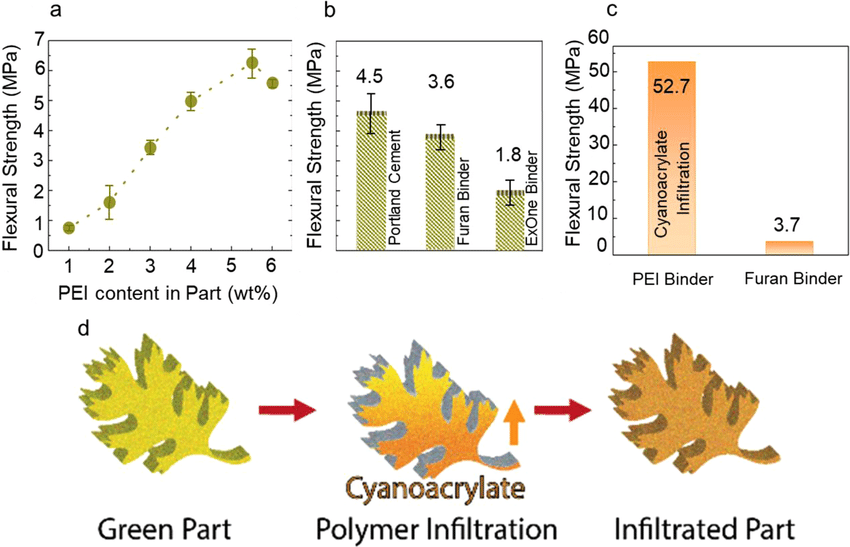
The Evolution of the Revolution
After disrupting the way foundry molds and cores are made, sand 3D printing is evolving. A research team at Oak Ridge National Laboratory developed a new binder that aids strong washout tooling
Sacrificial Tooling that Washes Out with Water
Strong washout tooling solutions streamline the production of aircraft ducting, pressure tanks, struts, mandrels and other hollow objects by 3D printing sacrificial tool cores in sand that wash out with water.
Learn more about x1 Washout