- Home
- Binder Jetting Resources
- Blog
ExOne Expert: Aldo Randazzo
ExOne Expert: Aldo Randazzo
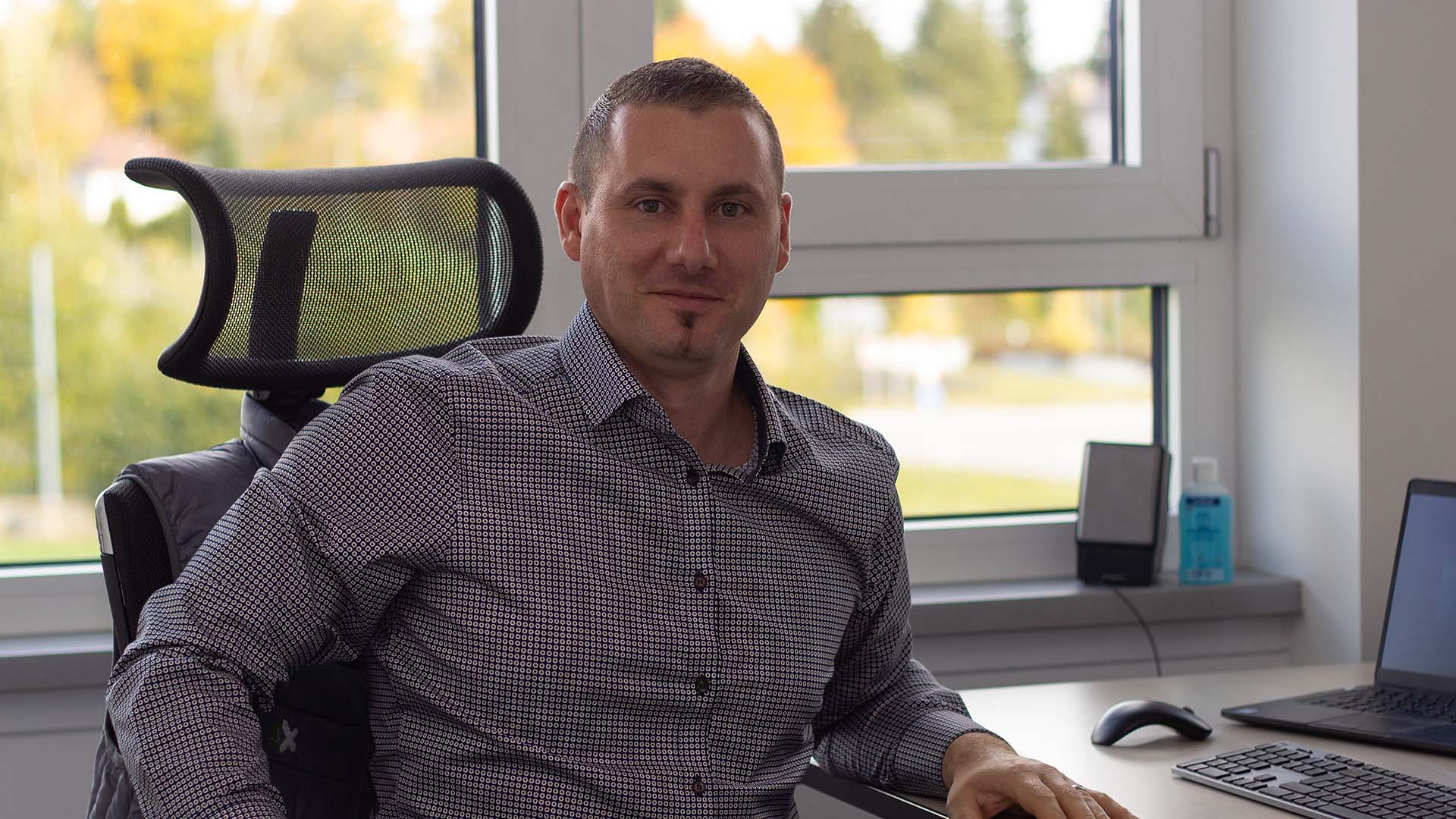
ExOne Expert: Aldo Randazzo
Our Lead Manager of Customer Applications has the essential casting knowledge to disrupt traditional foundry operations with solutions like 3D printing in core shops
The foundry industry is built on centuries of knowledge passed down through generations of workers. Having that inside knowledge of casting is essential to disrupting those traditional operations with new solutions like 3D printing. That’s why the foundry experience of Aldo Randazzo, Lead Manager of Customer Applications and Sand 3D Printing at the ExOne Adoption Center in Germany, is fundamental in helping convince foundries to try binder jetting technology. He emphasizes the importance of understanding not only how foundry 3D printing in core shops can enhance production, but how the various production methods foundries are currently using can be enhanced or eliminated with the introduction of a new process.
“If you discuss 3D printing with the customer you have to understand their current operations so we can compare with the traditional way. If we can explain the exact differences and the benefits of both, including where they can be combined, we can help them see the value quicker,” he says.
Helping foundries succeed is the passion that drives Randazzo. “The foundry is the beginning,” he said. “Nearly everything starts with foundry work and I really like to go to foundries, to see where it all begins.”
If we discuss 3D printing with the customer, we have to understand their current operations so we can compare with the traditional way. If we can explain the exact differences and the benefits of both, including where they can be combined, we can help them see the value quicker.
Aldo Randazzo
Lead Manager of Customer Applications and
Sand 3D Printing at the ExOne Adoption Center in Germany
Randazzo was attracted to the industry from an early age. As a young boy he toured a local foundry hosting an open house and was hooked. Laughing as he remembers seeing a melting shop for the first time, he said “In my mind it was very impressive because it’s hot with lots of iron is burning and you see strong men working on the furnaces and with liquid iron. Some of my friends thought it was a nightmare, but to me it was perfect.”
An apprenticeship through the advanced educational and training center at Heidelberger Druckmaschinen, a modern foundry in Europe, offered Randazzo his start in the industry. Gaining extensive core, melting, and metallurgy experience, he eventually earned a Foundry Master title. He led core shop operations, providing him a foundational understanding of production operations and traditional core technologies.
After adding additional technical certifications and an engineering degree (“I have nearly all the titles possible short of Professor or Doctor,” he jokes) Randazzo transitioned to product management and sales engineering roles for foundry suppliers. He credits this time for broadening his perspective because he traveled to visit foundry operations around the world. “I’ve seen a lot of different sites and various processes,” he said. “It’s not only impressive for me personally to see, but helpful to my work today to have a full picture of what foundry operations are like.”
It was during one of these tours when Randazzo first experienced the binder jetting process and started to learn the benefits of the technology for core shops. Working with the digital foundry experts today, he can confidently consult foundries on the many benefits of 3D printing in core shops.
3D printing isn’t the future, it’s today. But to be successful we have to show how they can become more competitive, especially when they can combine the benefits of traditional and digital manufacturing processes. If you show a customer you’re able to understand and explain new things in a way that makes sense to them then we’re really able to transfer the knowledge and work out the benefits for their operations. At the end of the day, they understand the cost of missing out on reduced production times, improved quality, automation, and all the other benefits we can offer them.
It isn’t just for industry customers Randazzo shares the benefits of 3D printing with, supporting educational initiatives like Foundry Skills. Thinking back to the strong impression experiencing a foundry first-hand made on him as a youth, he said, “If you can see it, this says more than a thousand words.” Emphasizing reaching out to the next generation of foundry workers he continued, “If you see a process directly on a platform like this then more people can really see how it works in a way that captures a modern audience. So together we are able to bring this knowledge to schools and education centers, to universities and even the employees of our customers, then everybody grows up with ExOne and sand 3D printing and we can really take it to the next level.”
And new challenges are already keeping Randazzo busy, as increasing numbers of innovative sand 3D printing applications are supported by the ExOne Adoption Center in Germany. “We’re seeing the market grow every year with more and more applications for architecture, home goods, and other products,” he said, referencing work with companies like Sandhelden sinks and Deeptime speakers, artistic designs 3D printed in sand before infiltration into durable products.
“We have virtually no limitations, it’s exciting to see where we keep going with the technology,” he concluded.
Learn More from Real Foundries and Core Shops
Watch video of 3D printing in core shops and read stories of foundries successfully implementing binder jetting in their operations
success stories