Blog

ExOne Strengthens Commitment to Foundries Under New Ownership
With a renewed focus and dedicated resources, ExOne reaffirms its role as a trusted technology partner for metalcasters.

Anzu Partners Affiliate To Acquire ExOne
The acquisition ensures stability and consistency of operations for customers, suppliers, and employees in the future.
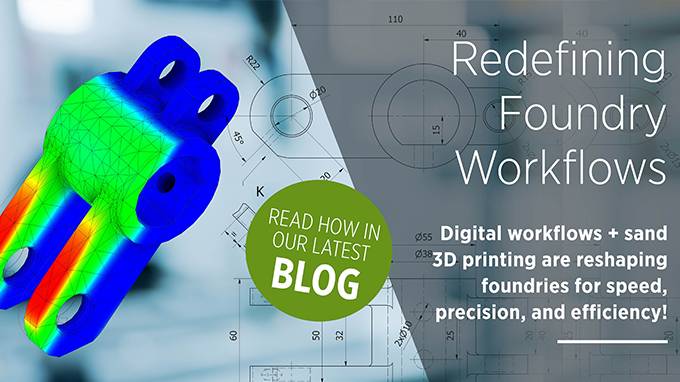
Streamlining Casting Workflows with Sand 3D Printing
Discover how digital workflows simplify castings - cutting lead times and improving labor efficiency in foundry operations.
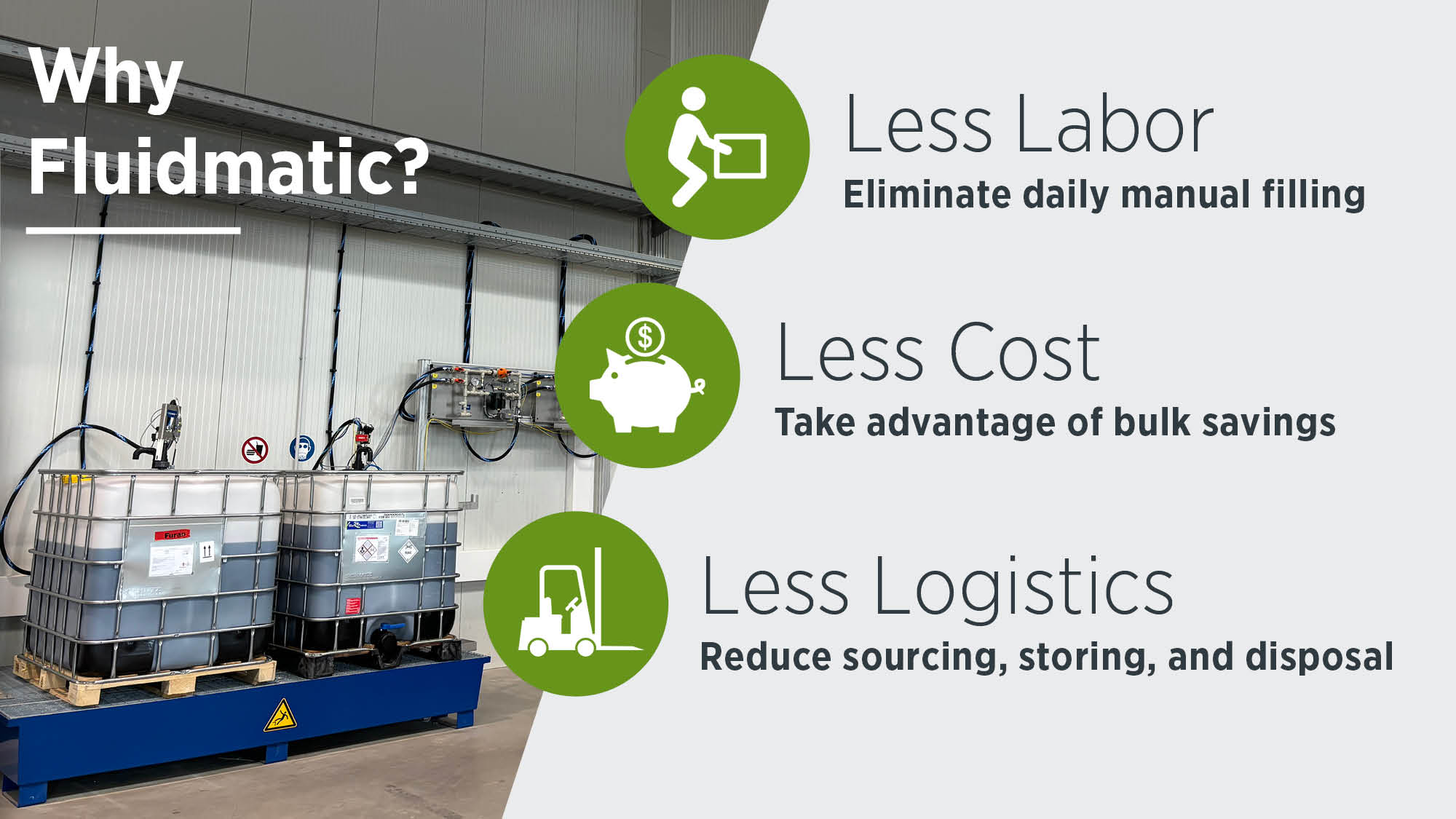
Accessory to Efficiently Manange Fluids for Fleets of 3D Printers
Automate the automatic supply of liquid binder and cleaner to up to four machines to reduce costs, labor, and logistics
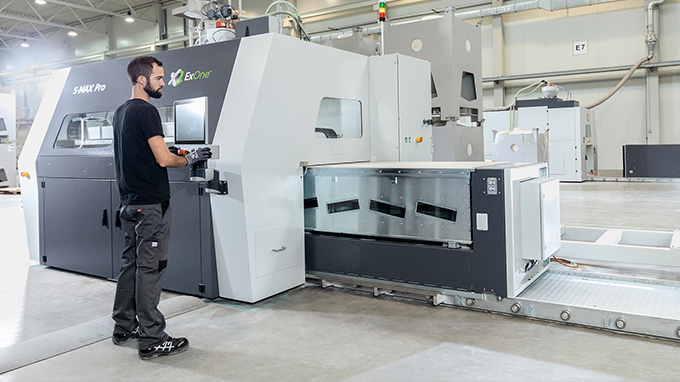
Embracing the Future Foundry Workforce
3D printing revolutionizes sandcasting and attracts a new generation of workers to the foundry with benefits like creative freedom and environmental responsibility.

Guide to Binder Jet Sand 3D Printing for Foundries
What is sand 3D printing, how is it used, and what industries benefit? Learn more in this guide to 3D printed sand.
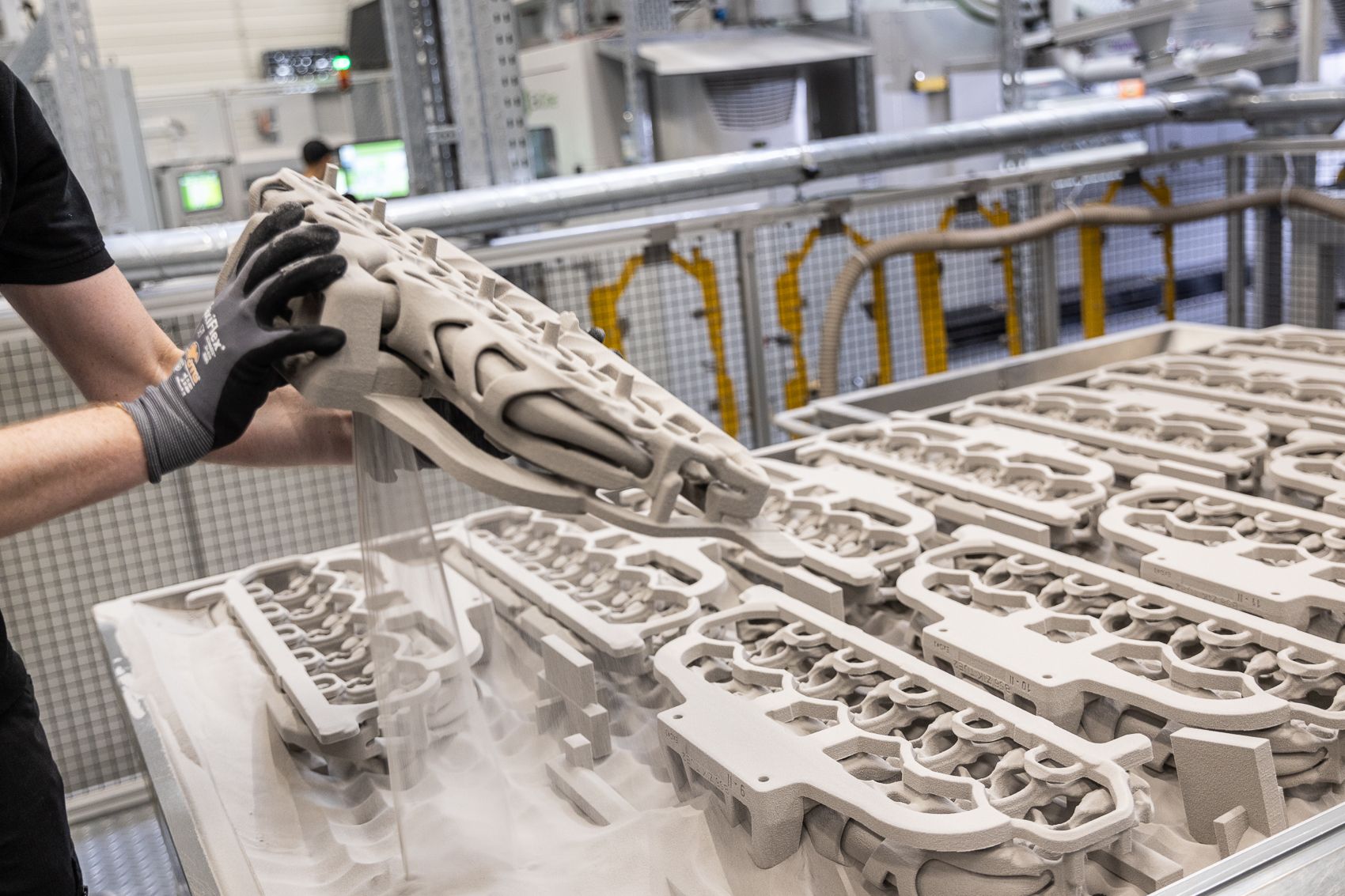
Inside the Pioneering AM Journey of BMW and ExOne
Learn how ExOne’s binder jet 3D printing technology helps BMW make its sustainable manufacturing vision a reality in serial production.
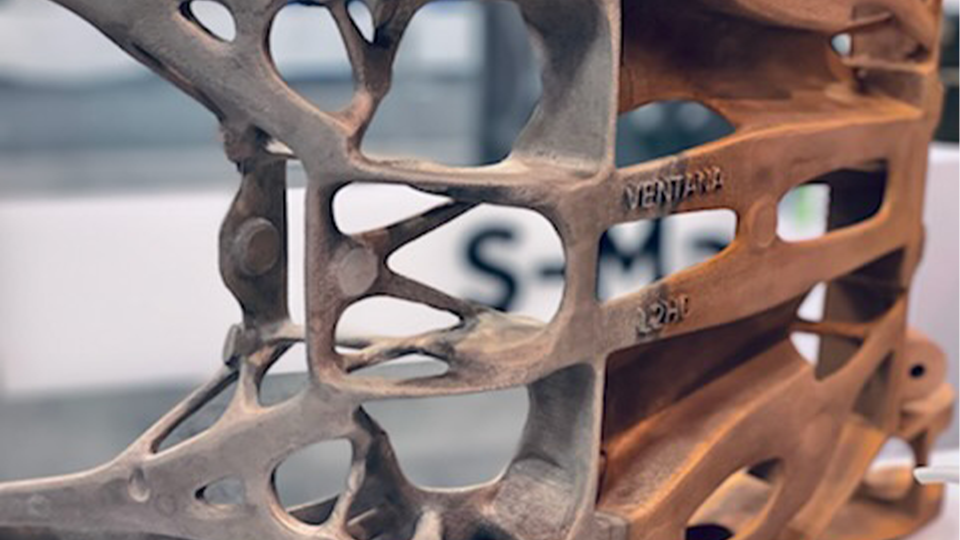
Pushing Lightweight Solutions to Market with Digital Casting Technology
Foundries are offering innovative lightweight solutions with digital casting technology
Tip sheet: Why cast metal with 3D printed sand?
From faster delivery times and new design freedoms to labor shortage solutions and overall cost savings, here's our top top ten benefits of 3D printing for sandcasting foundry operations
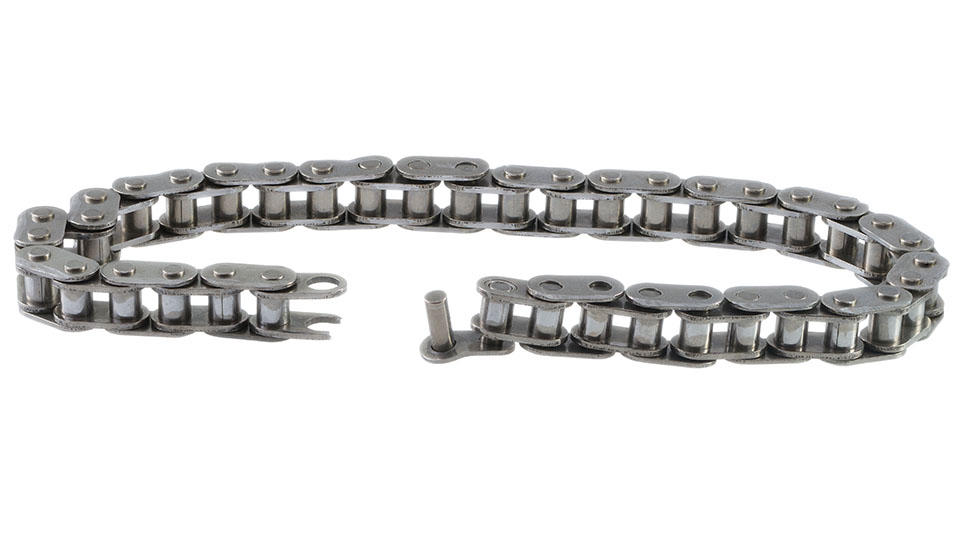
Digital Foundries Deliver Critical Replacement Castings, Fast
Sand 3D printing strategies support de-risked supply chains by producing foundry molds and cores direct from digital models that drastically decrease lead times, tooling investment and casting defects
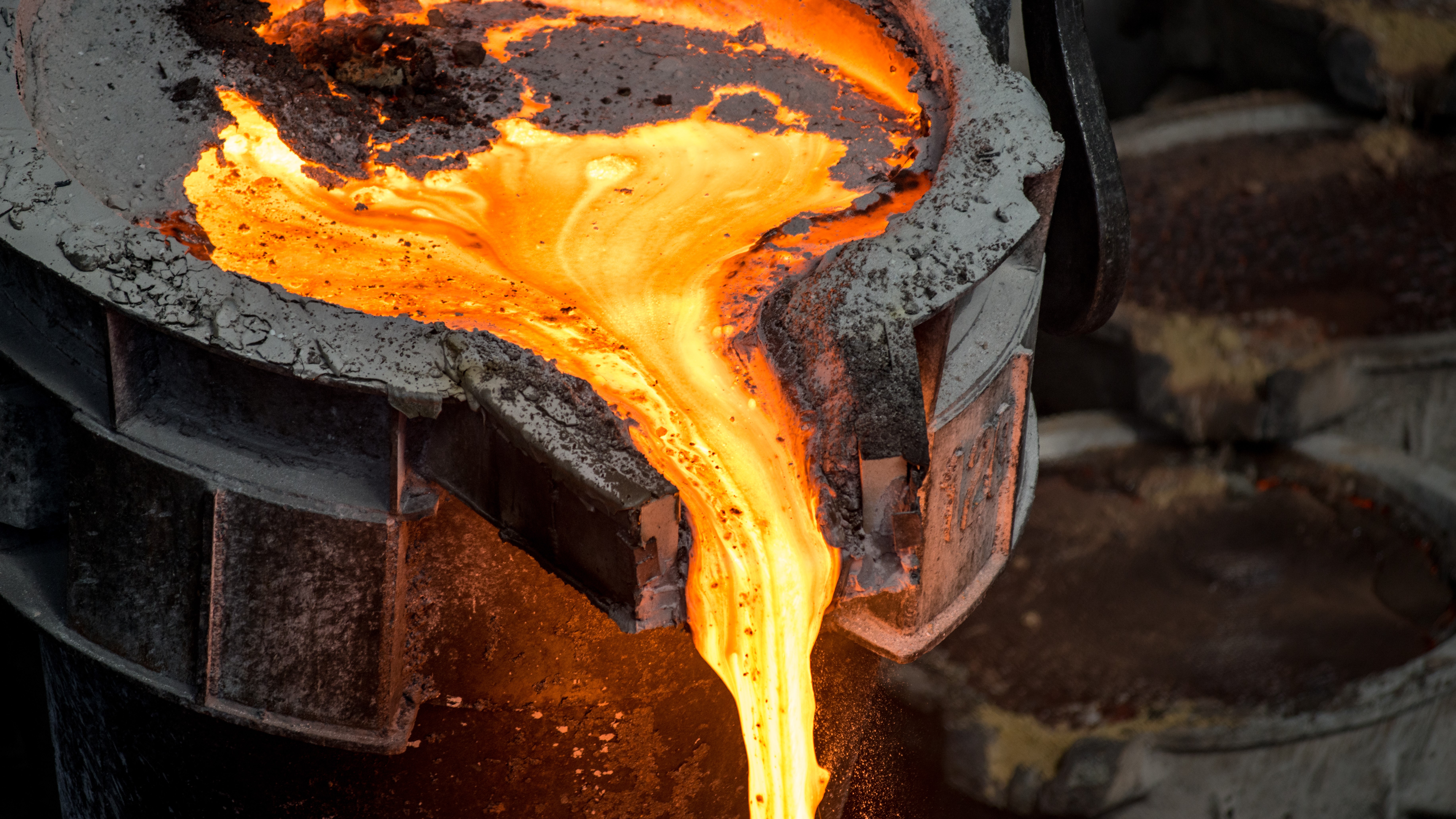
Keeping Foundries Flowing
Sand 3D printing helps foundries build resilient supply chains with flexible core and mold production, without the cost of producing or storing traditional tooling
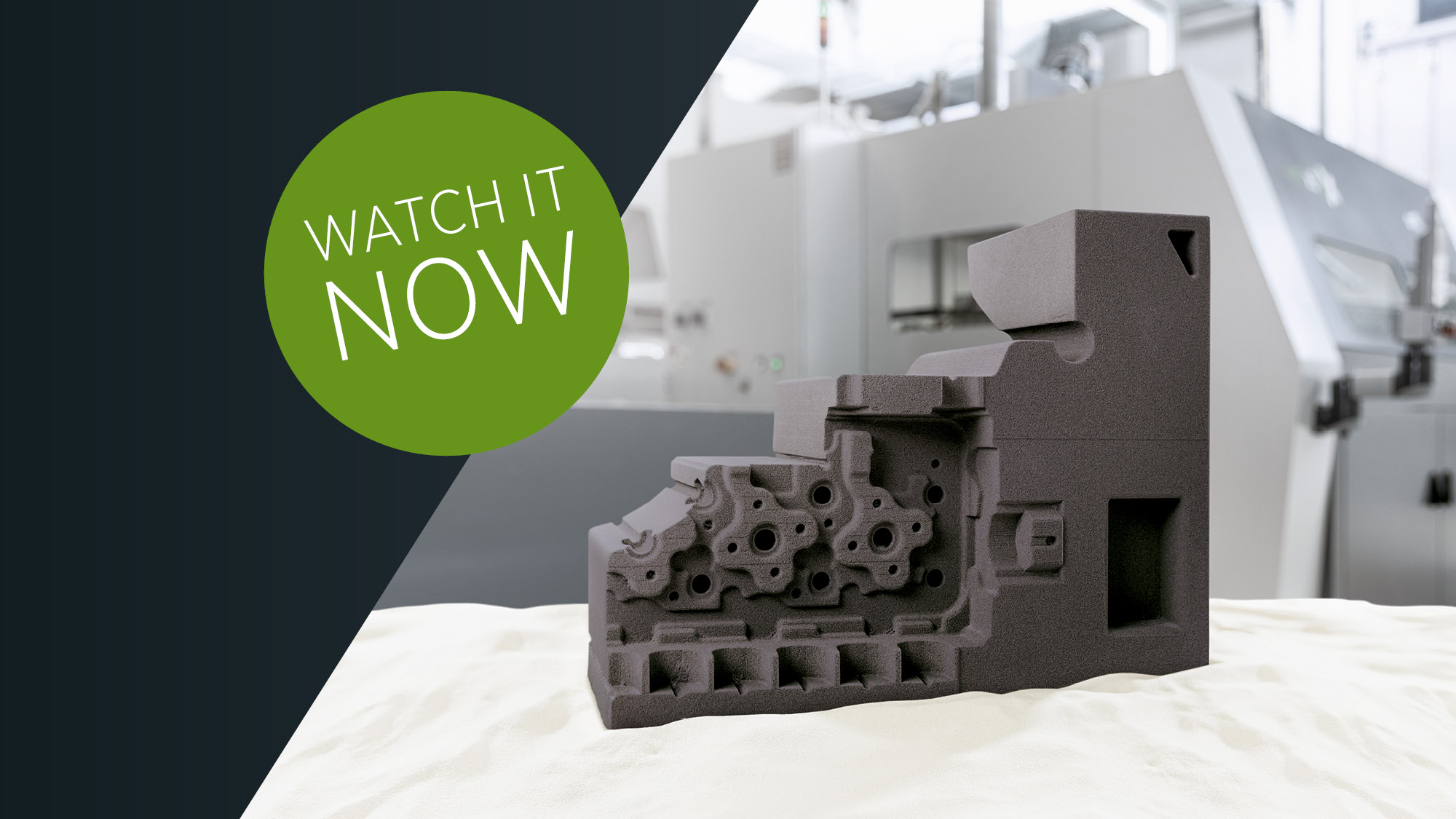
On-Demand Webinar: Sand 3D Printing with Binder Jetting Technology
Discover how sand 3D printing with binder jetting technology can transform your casting business. Learn about the business model of digital casting. Exclusive for the Indian market.
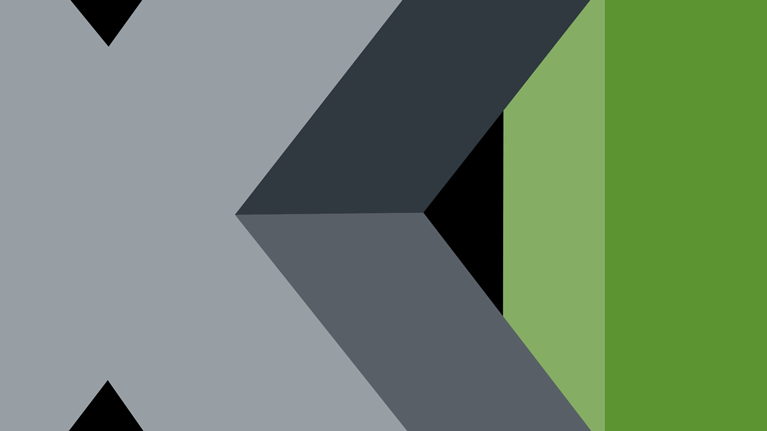
Turkish Foundries invest in 3D Printing
How three turkish foundries meet the challenge as key roles in international supply chains
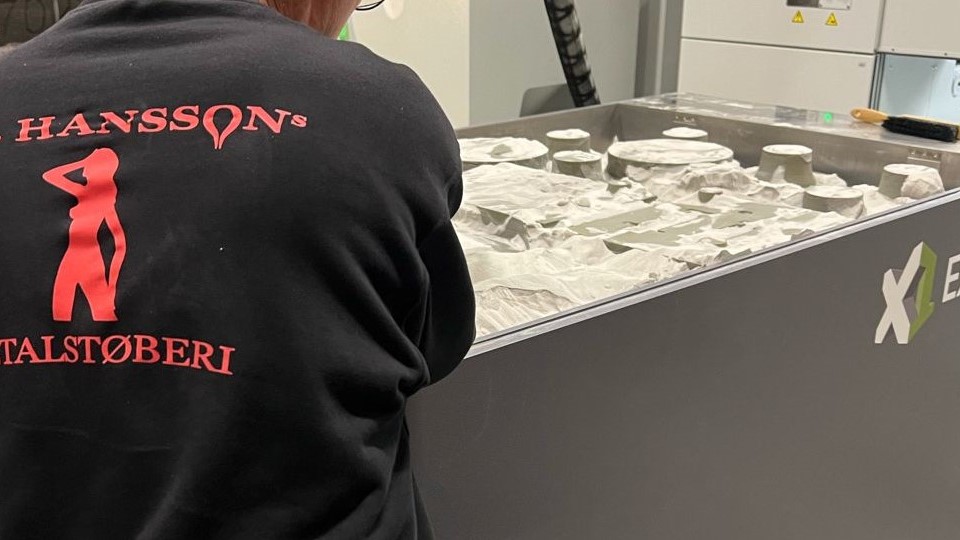
Case Study: K.B. Hanssons
First ExOne sand binder jetting system in Denmark offers on-demand precision sandcasting tooling with reduced delivery times
.jpg)
ON DEMAND: APAC Webinar Series
Learn more about ExOne sand 3D printing technology and the benefits to foundries in this webinar series focused on the challenges of the Asia-Pacific region.
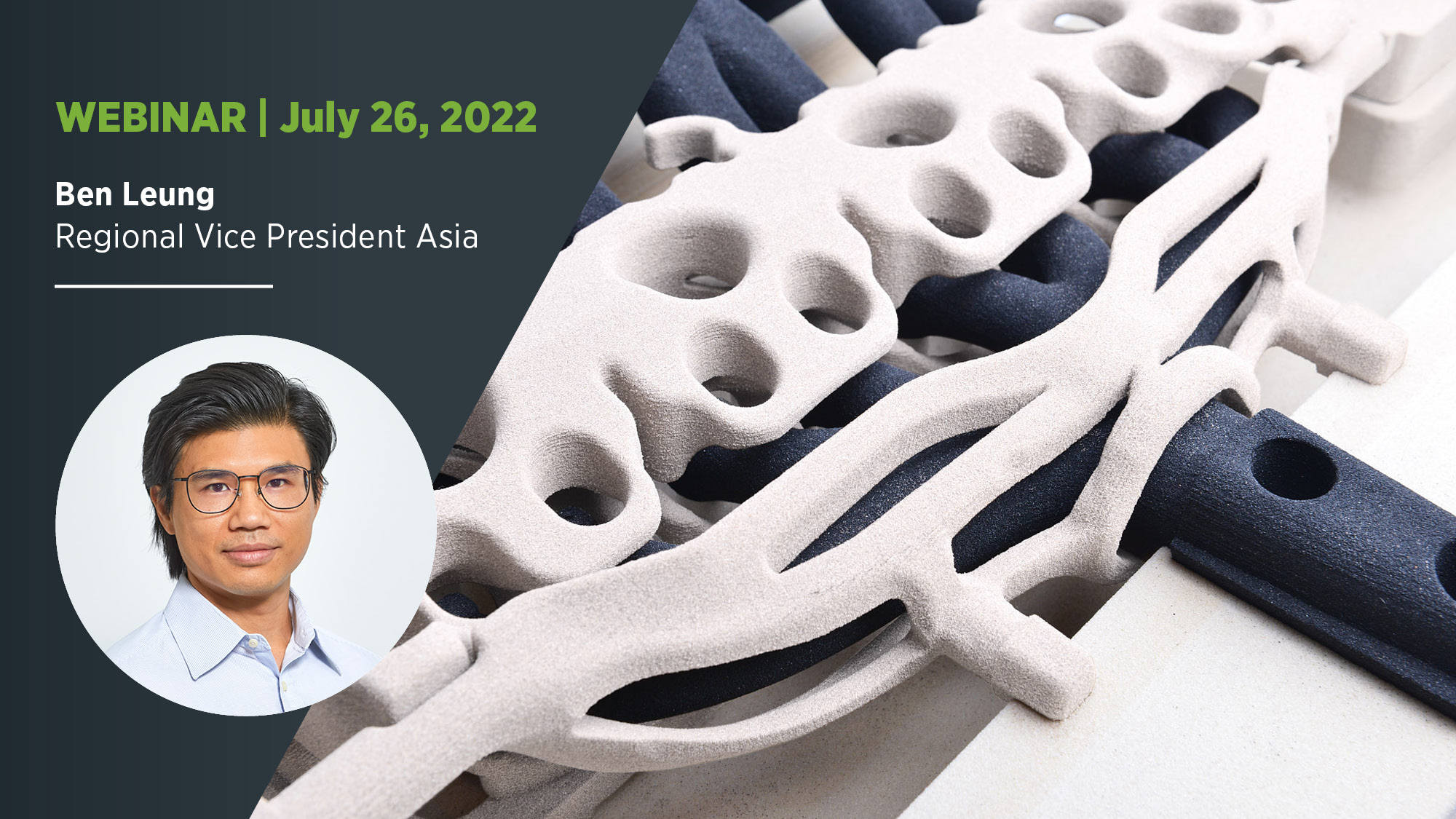
WEBINAR: Sand Binder Jetting - How does it work?
Attendees will learn all about this AM process, from the CAT File all the way through the casting process. You will be able to get insights into different binder types and insights on the day-to-day operation of an S-Max Furan binder jetting system told by 3D printing super-user, Nattinee Valun-araya, Head of Engineering at Speed 3D Mold.
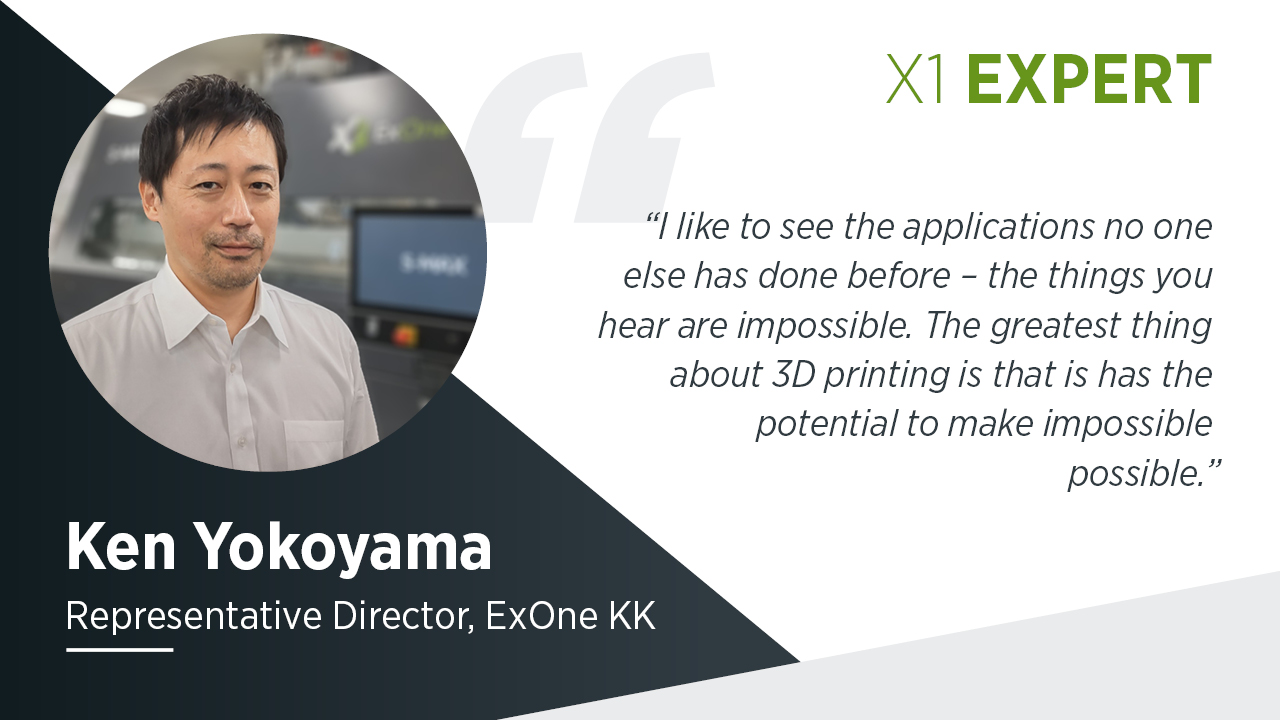
X1 Expert: Ken Yokoyama
Our regional sand 3D printing experts support foundry adoption around the world and play a global role in pushing groundbreaking binder jetting innovations
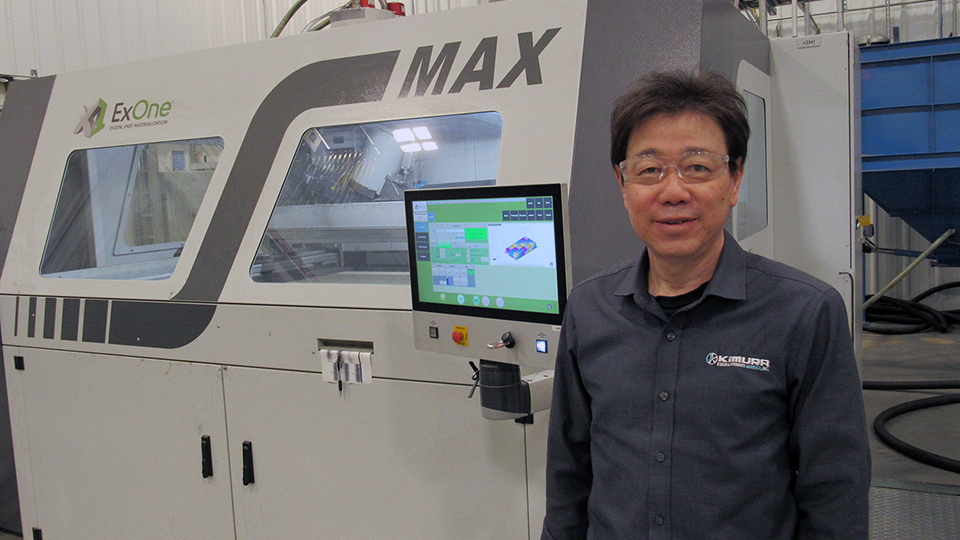
Kimura Foundry Group Purchases 10th Desktop Metal Sand Binder Jet Additive Manufacturing System
Following the purchase of a new S-Max®, Kimura Foundry Group now owns the largest number of ExOne systems globally
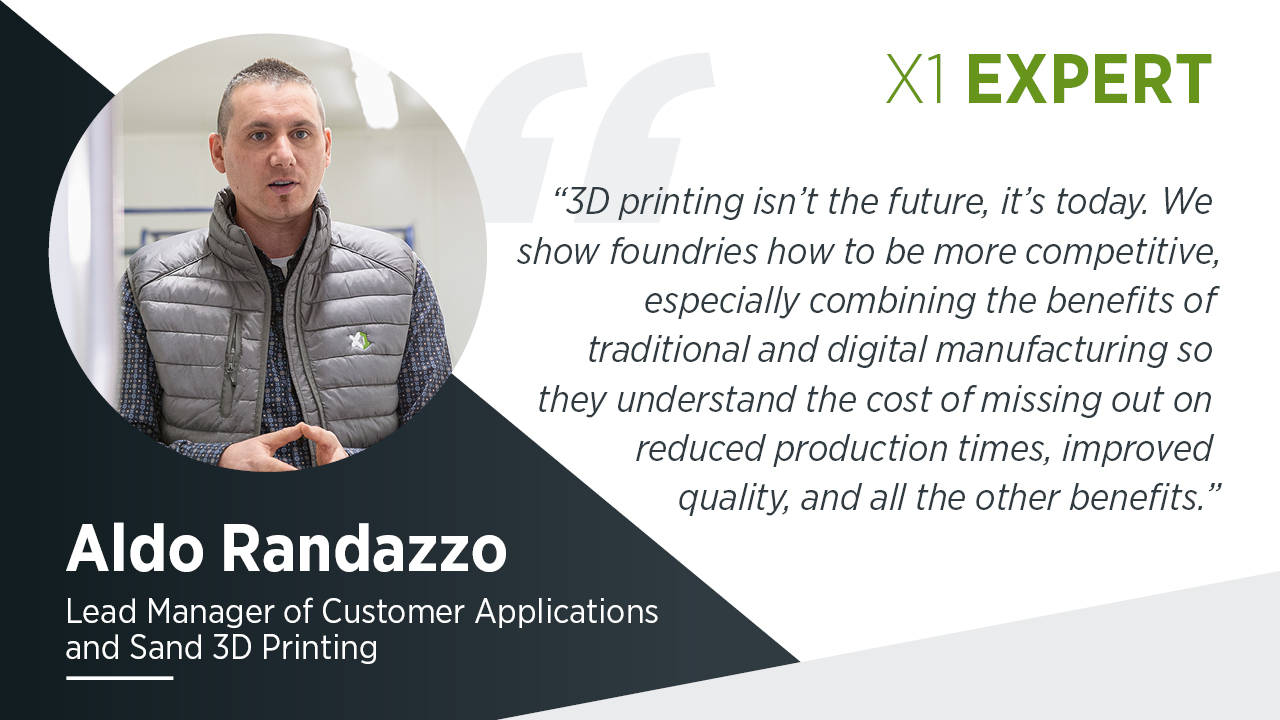
ExOne Expert: Aldo Randazzo
Our Lead Manager of Customer Applications has the casting knowledge essential to disrupt traditional foundry operations with new solutions like 3D printing
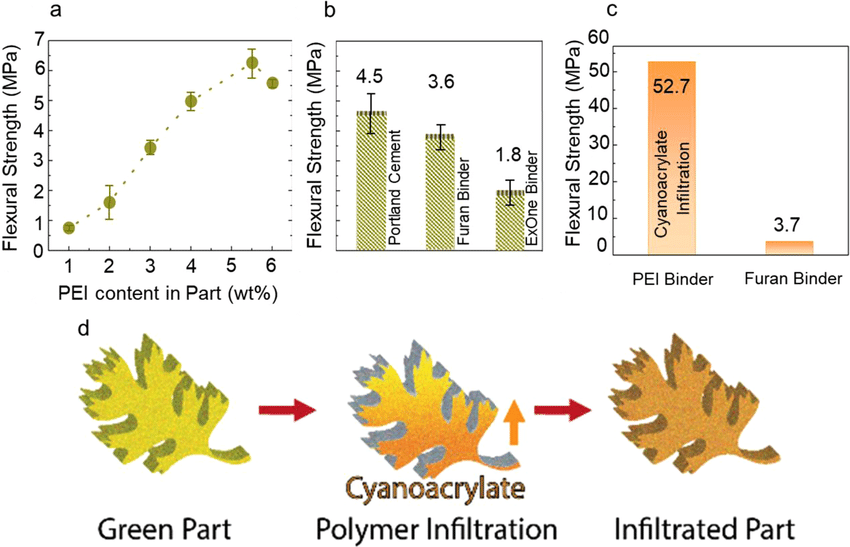
The Evolution of the Revolution
After disrupting the way foundry molds and cores are made, sand 3D printing is evolving. A research team at Oak Ridge National Laboratory developed a new binder that aids strong washout tooling
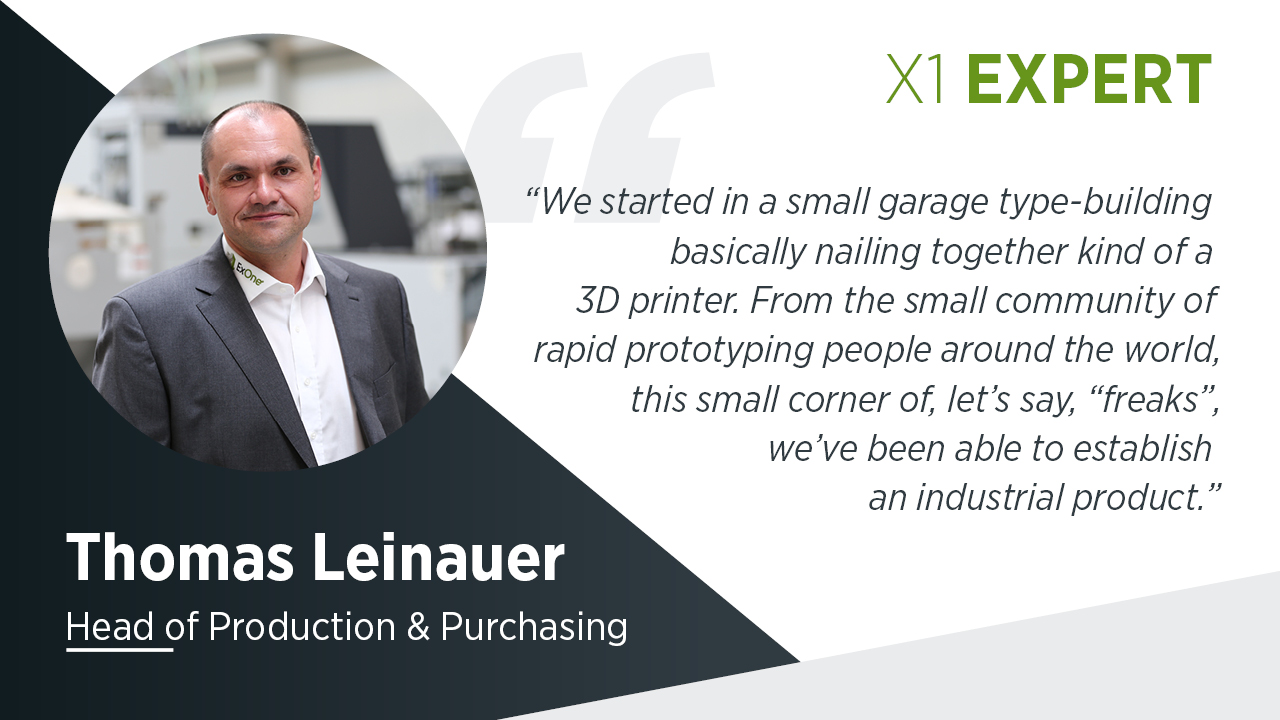
ExOne Expert: Thomas Leinauer
Our Head of Production & Purchasing has been key to growing the company for nearly two decades
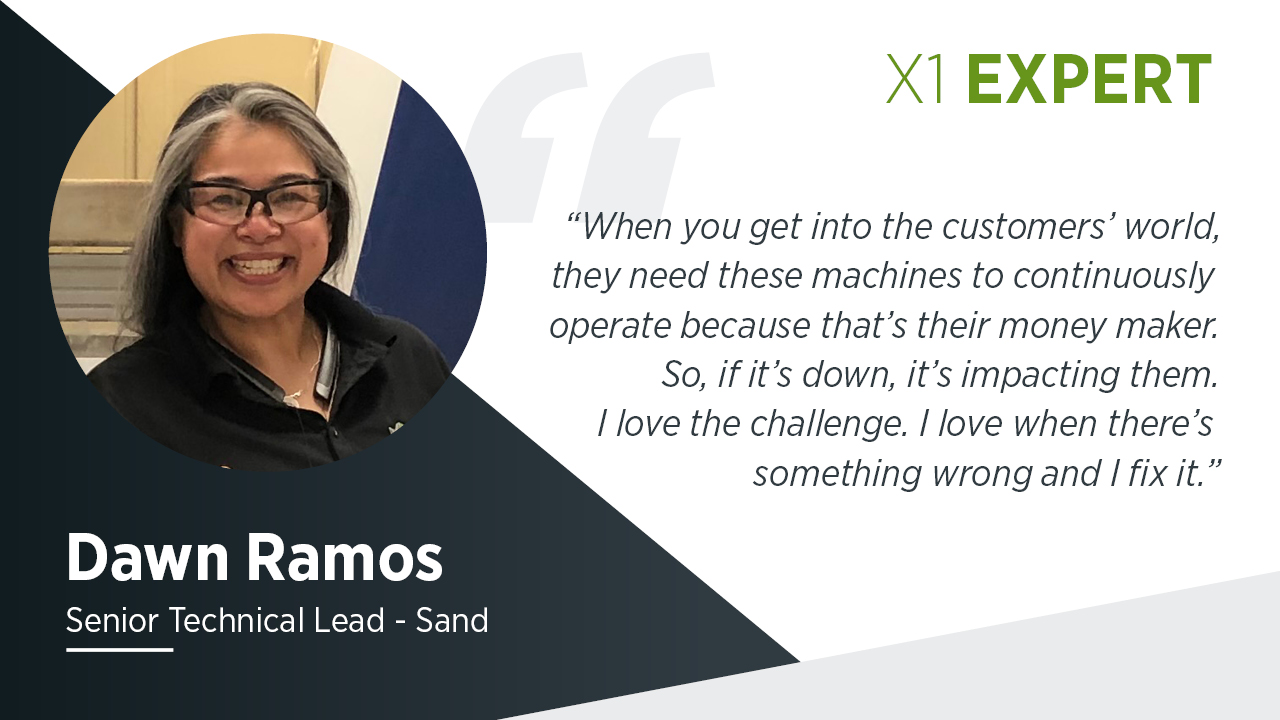
ExOne Expert: Dawn Ramos
Our Senior Technical Lead has worked on systems from the first metal machines to the newest sand binder jetting installs
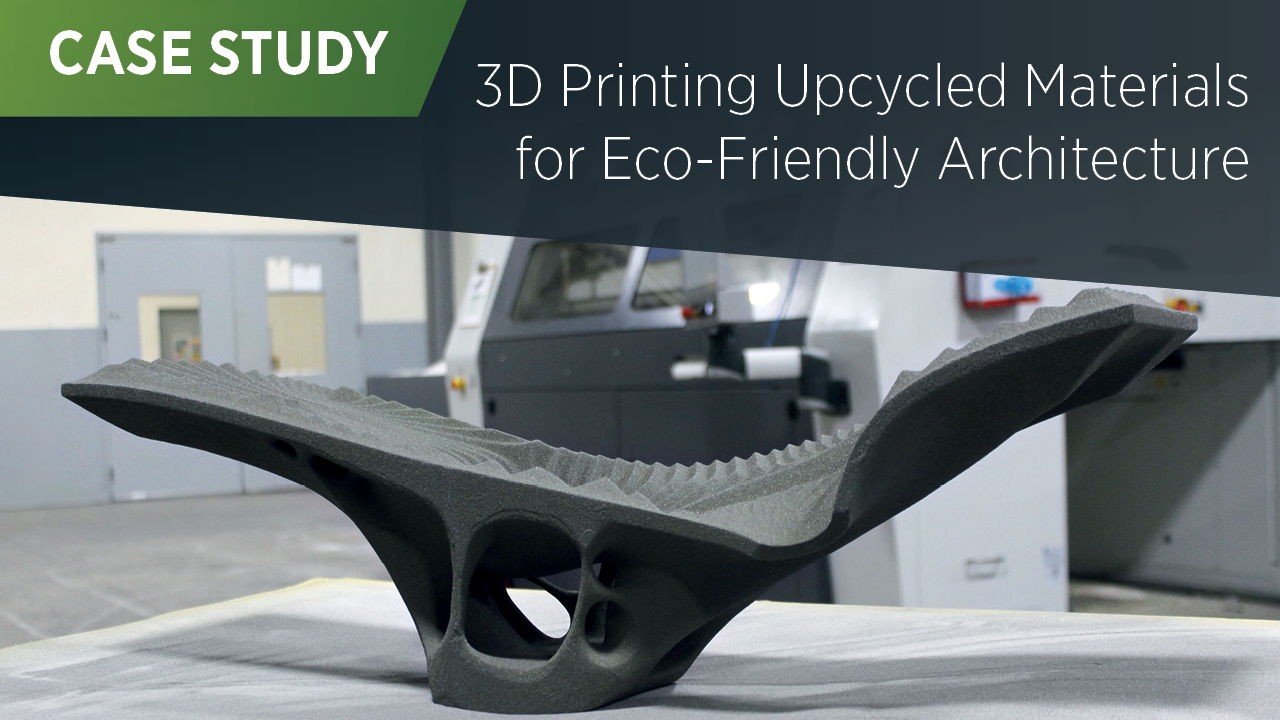
Reinventing Eco-Friendly Architecture and Upcycled Materials with ExOne Binder Jetting
The design research team is shaping the future of building design by remodeling granular materials such as concrete into new forms that show the potential for materials reuse and sustainable designs enabled by ExOne binder jet 3D printing.
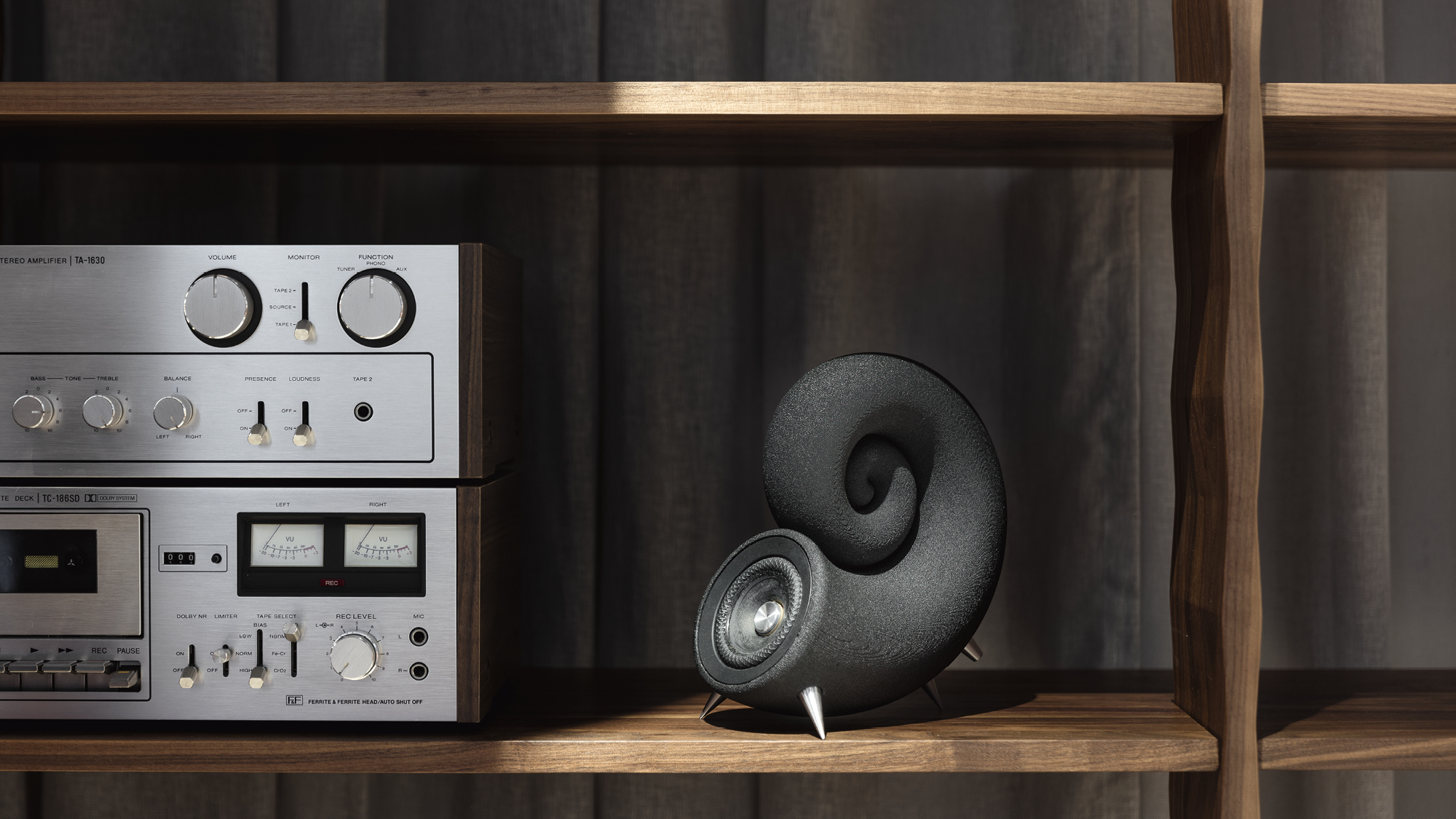
Turning Sand into Sound: 3D Printed Speakers
How a small startup in Czechia is challenging the giants of the audio industry with the help of 3D printing
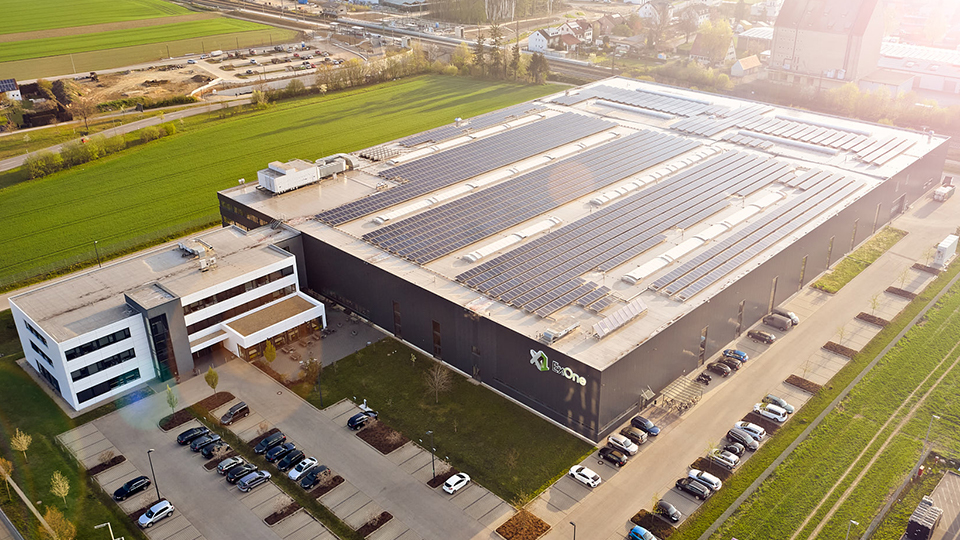
Living Our Value of Sustainability
ExOne's German location features solar panels that provide 75% of the facility's energy.
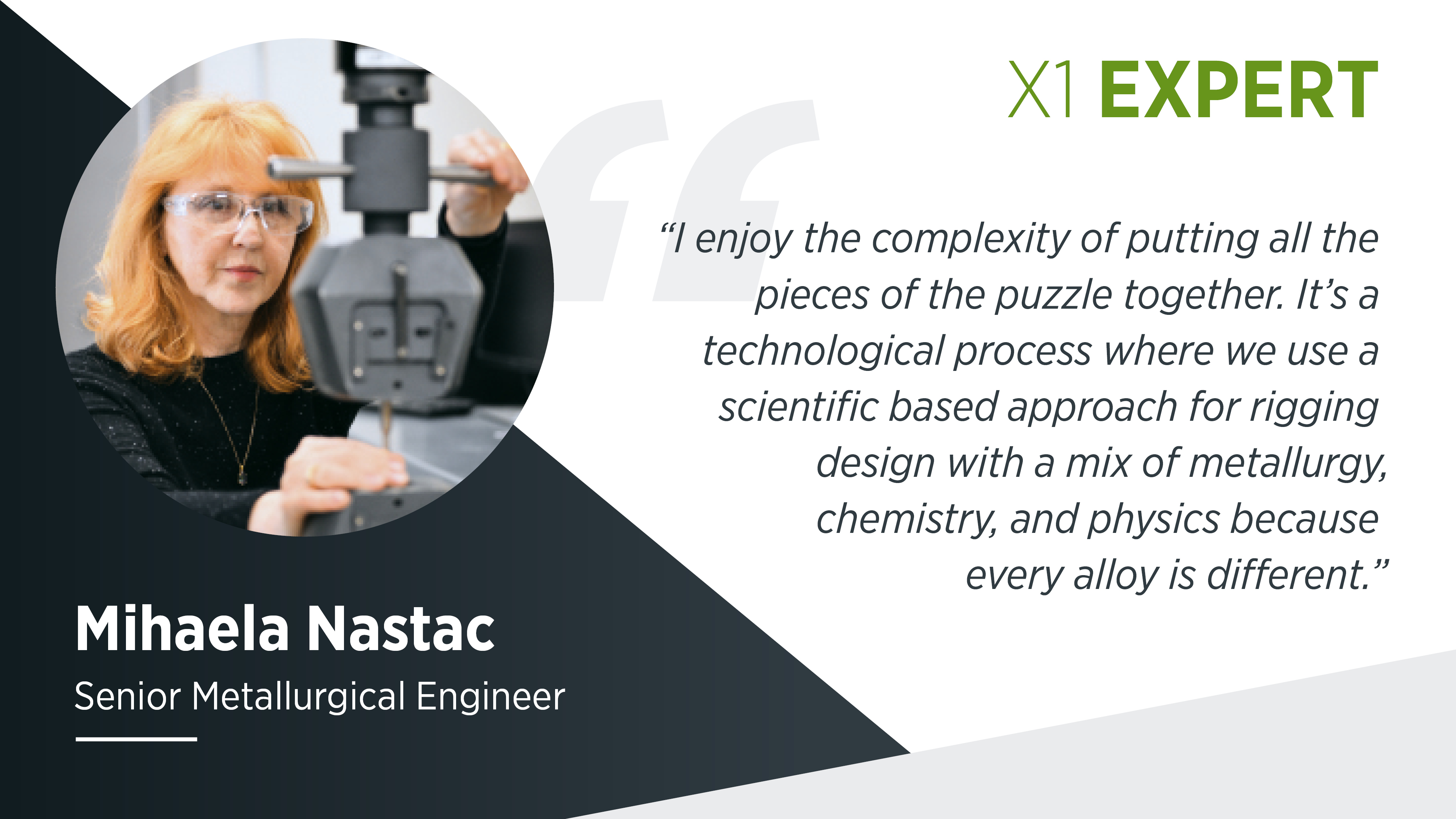
ExOne Expert: Mihaela Nastac
In 15 years with ExOne, Mihaela Nastac has established a reputation as the digital casting expert. We spoke with her about her role supporting customers and how she enjoys working to develop each project step-by-step.
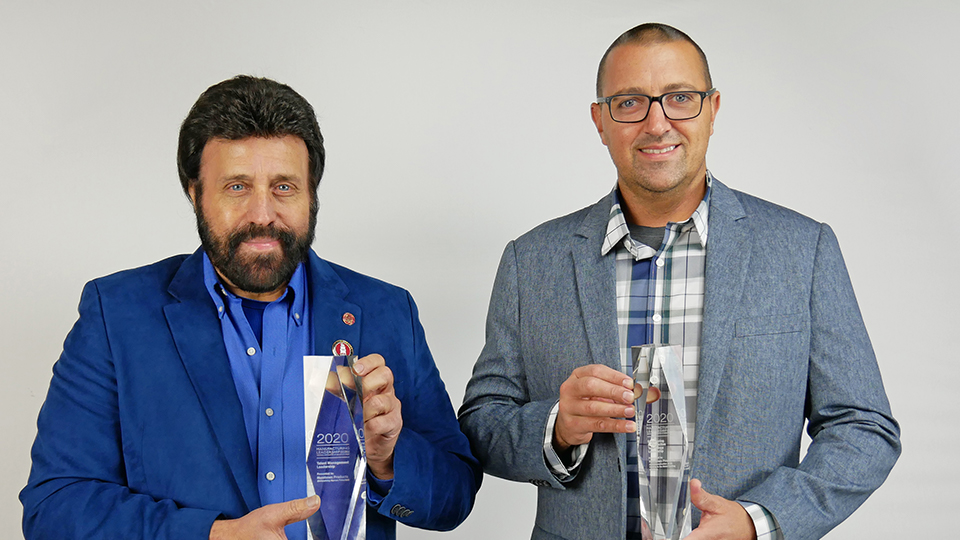
Humtown Wins 2020 Manufacturer of the Year Award for Sand 3D Printing Expertise
Humtown Products Wins 2020 Manufacturer of the Year Award for Sand 3D Printing Expertise
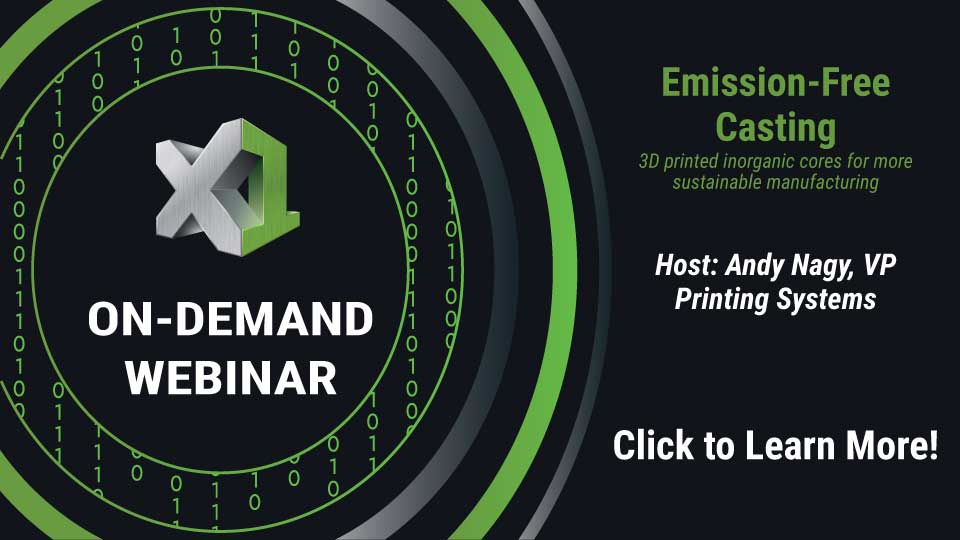
ON-DEMAND WEBINAR: Emission-Free Casting
In this webinar, learn why sand 3D printing with inorganic binders opens new opportunities to produce sand cores in a resource-friendly way.
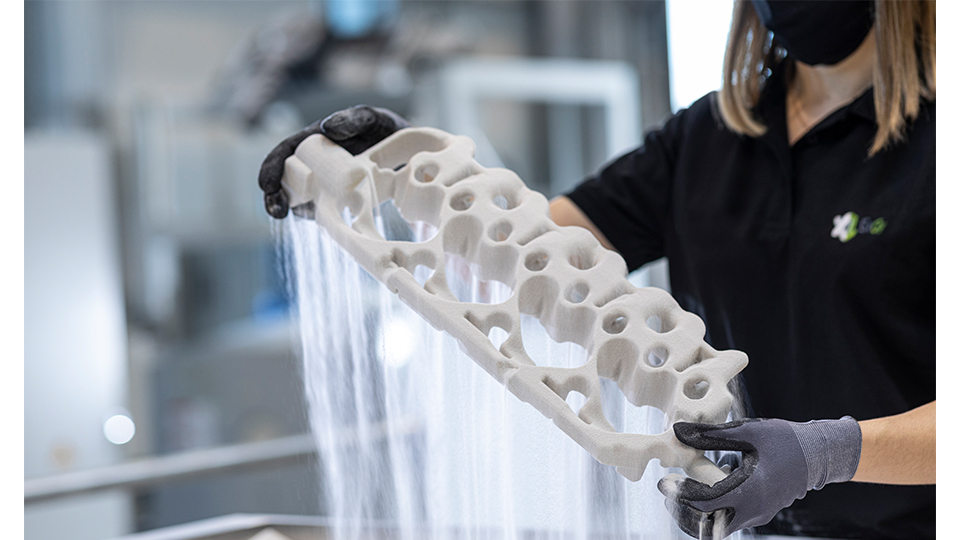
WEBINAR: Modernizing 3D Sand Core Production With Inorganic Binder
More sustainable 3D printing of cores is now possible with binder jet printing of inorganic binder.
Register for the Webinar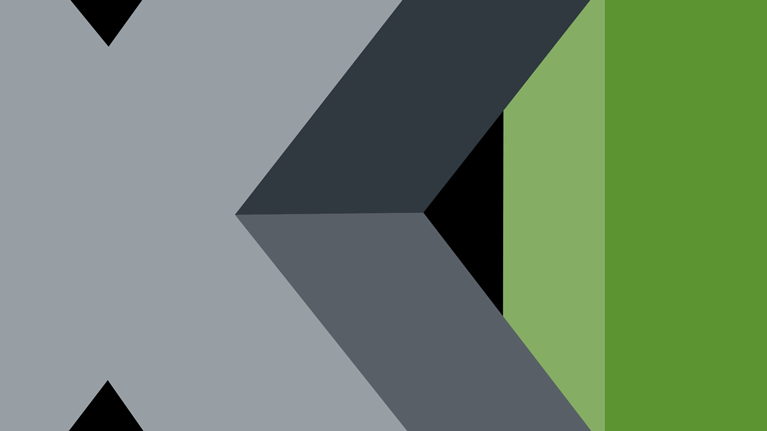
ExOne Adds ABC Corporation as 3D Printer Sales Partner in South Korea
ABC Corporation is committed to helping modernize foundry operations and expand sustainable technologies in the metalcasting industry.
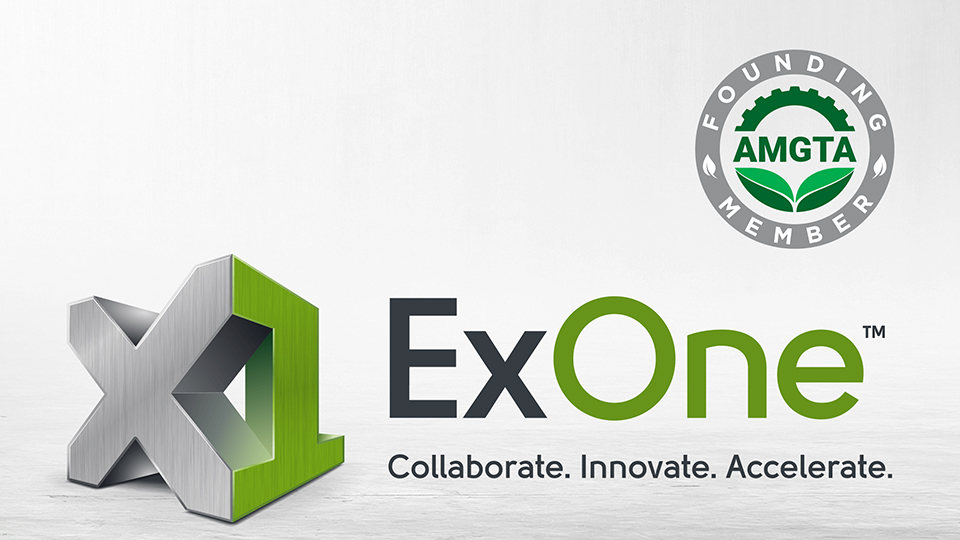
ExOne Joins the Additive Manufacturer Green Trade Association as a Founding Member
AMGTA promotes the environmental benefits of additive manufacturing (AM) in a variety of ways, including through rigorous and independent ongoing research.
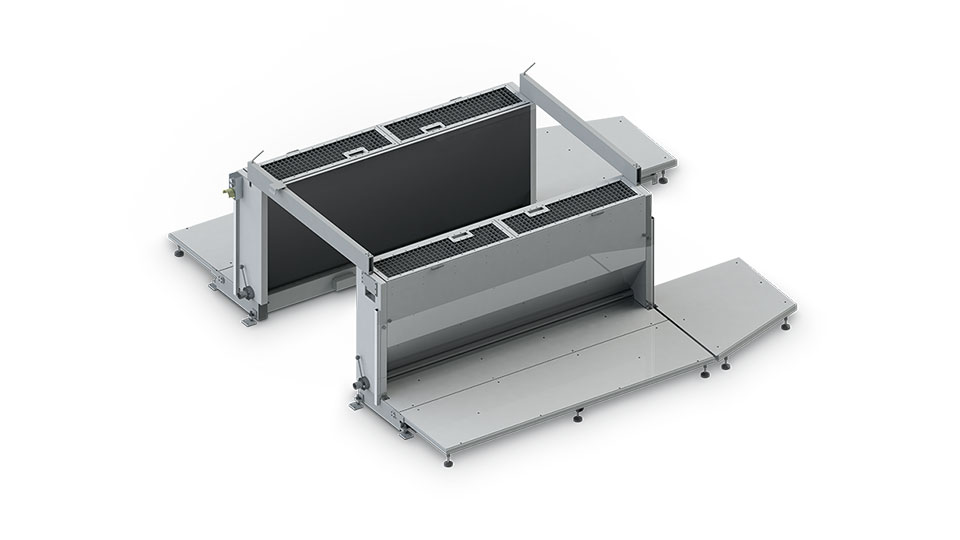
ExOne Enhances Productivity of Industrial Sand 3D Printers with New Desanding Station
ExOne announced the launch of a new desanding station for use with the industrial S-Max® and S-Max Pro™ sand 3D printers, the company’s most popular family of printers.
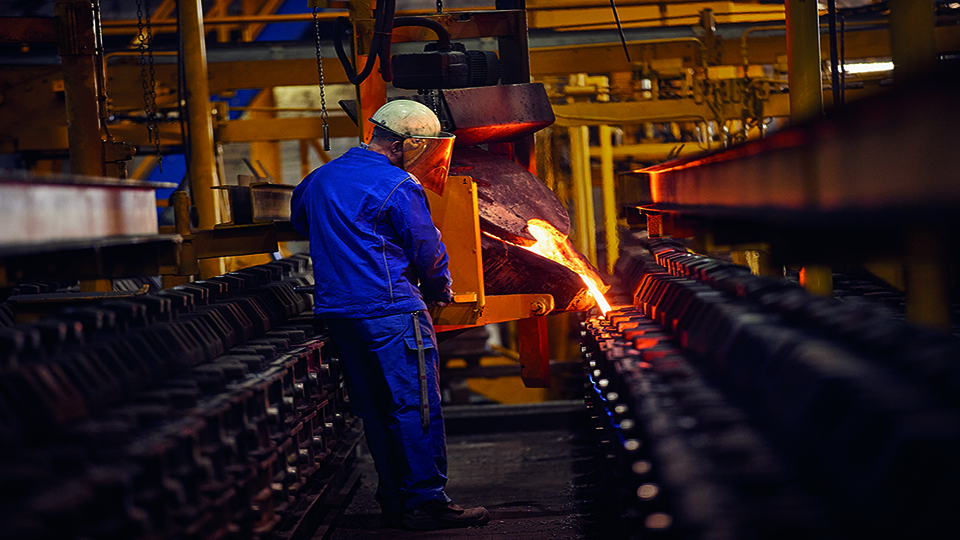
Innovative and Sustainable: A Step into the Future with 3D Printing Technology
Eisengiesserei Mezger, a Swiss iron foundry, expanded its services with a highly automated 3D printing system from ExOne – making the jump into new markets.
Case Study: Eisengiesserei Mezger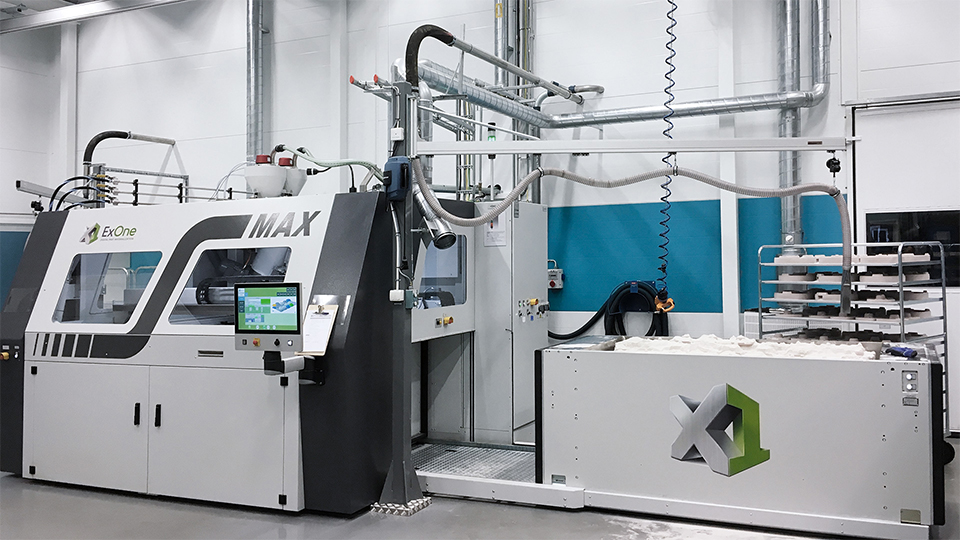
3D Printing Technology Dramatically Improves Manufacturing of Impellers
ExOne’s binder jetting printing technique simplifies production at the world’s leading water technology company, Xylem.
Case Study: Xylem Water Solutions Manufacturing AB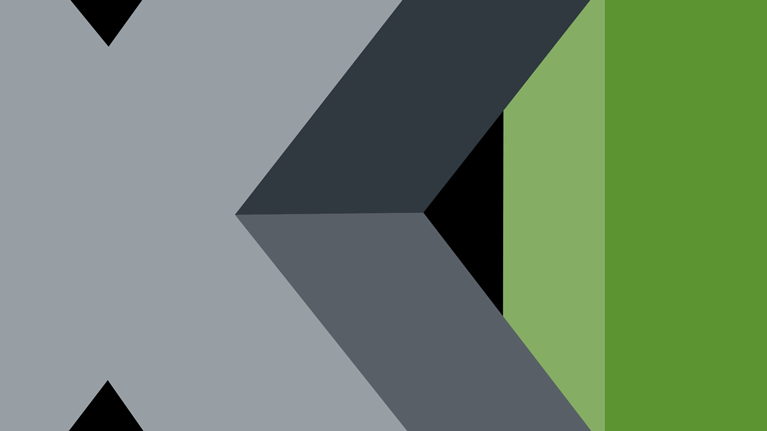
ExOne to Optimize Sand 3D Printers for Use with ITOCHU Ceratech Corporation’s Cerabeads®
Cerabeads® are a premium ceramic foundry sand used to create molds and cores for metal casting high-value products in the automotive, oil & gas, mining and construction industries.
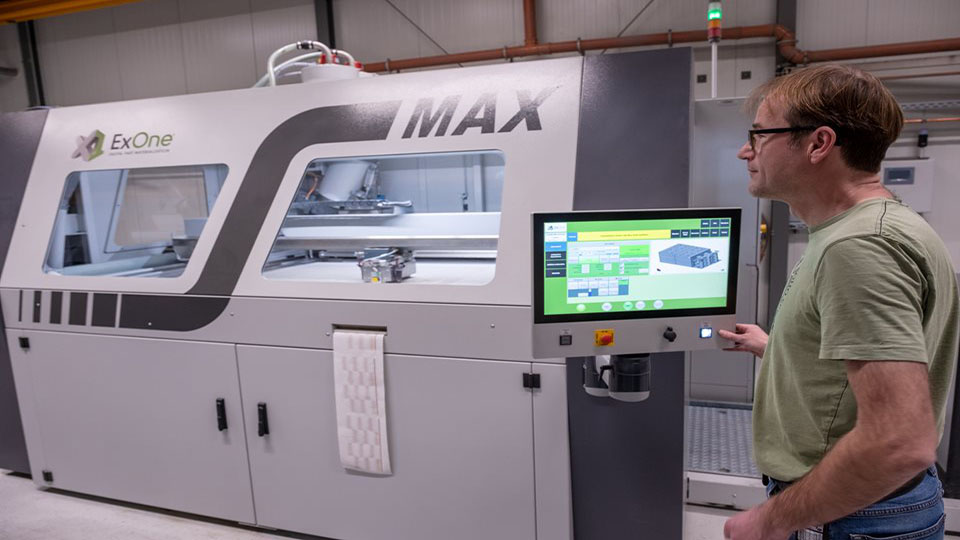
New Perspectives Through 3D Printing
The prototype casting company Grunewald in Bocholt, Germany, invested in a 3D sand printer made by ExOne at the end of 2018. After more than a year, the payoff has been substantial.
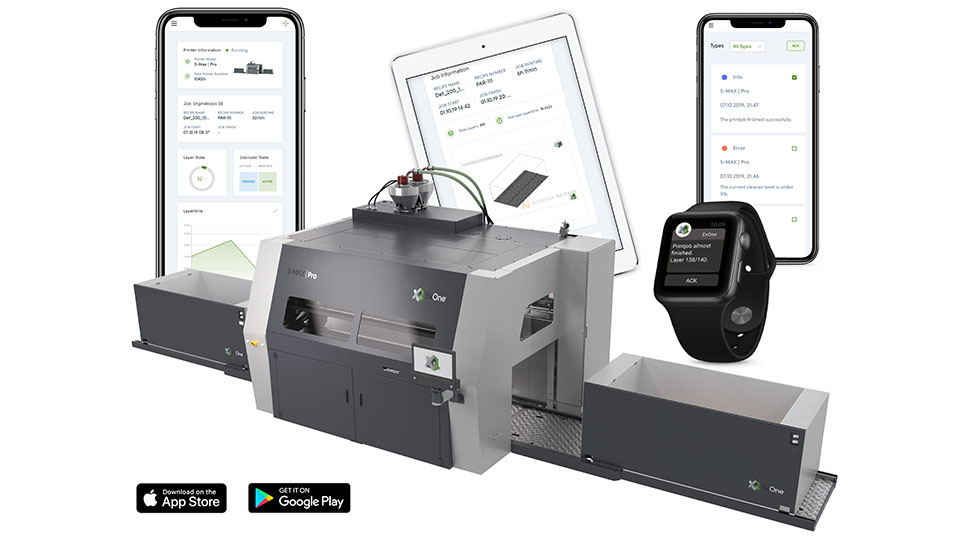
ExOne Launches New Scout App to Monitor Industrial 3D Printers
The ExOne Company announced the launch of ExOne Scout, a secure Industry 4.0 app that provides real-time machine monitoring and analysis of production 3D printers on a wide range of digital devices, including smart phones and watches.
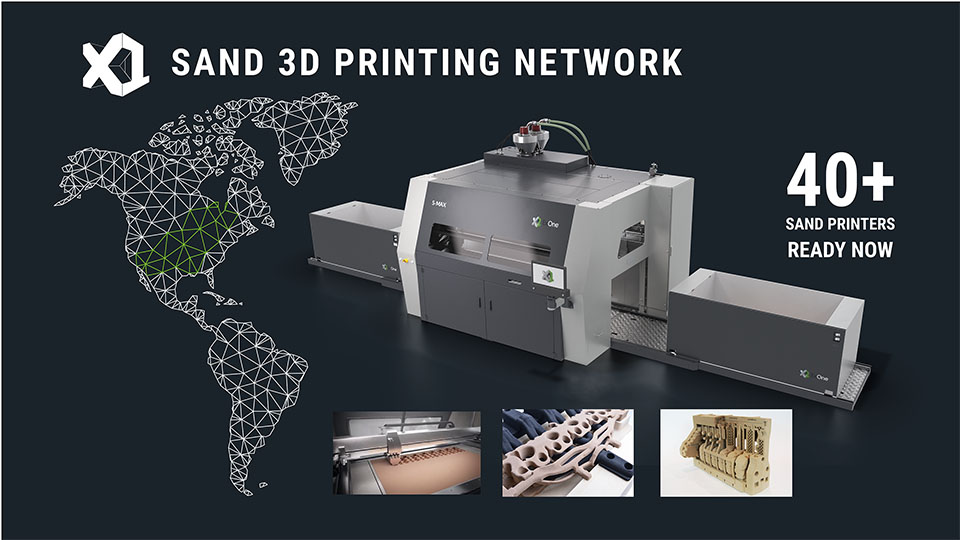
ExOne Launches New Sand 3D Printing Network
The ExOne Company announced the creation of a Sand 3D Printing Network in North America, which aerospace, automotive, agricultural and other manufacturers can use to tap the benefits of 3D printed sand molds and cores for high-value metal casting projects.
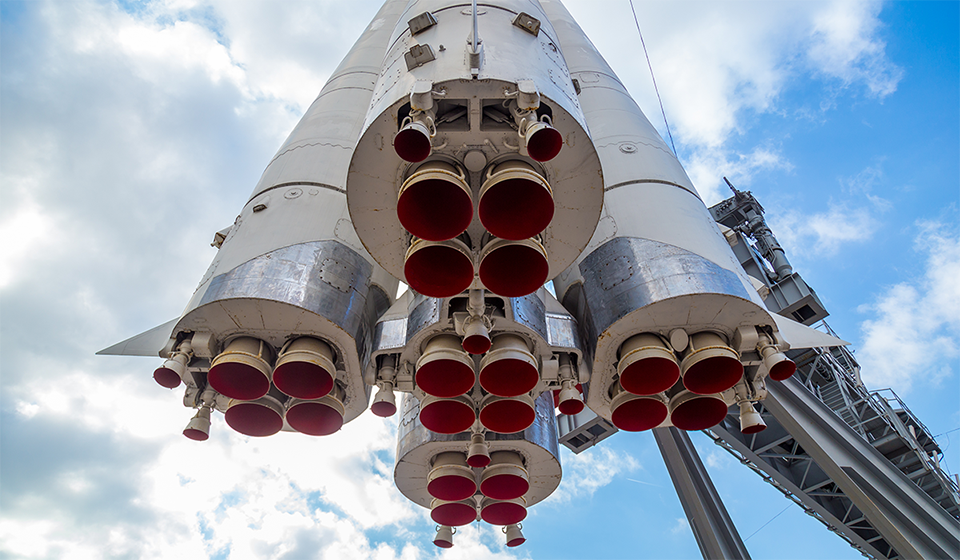
OneCast Design Services for Complex Metal Castings
ExOne's world-class 3D metalcasting experts are helping some of the world's most mission-critical manufacturers deliver on their metal casting goals with ease.
ExOne OneCast Services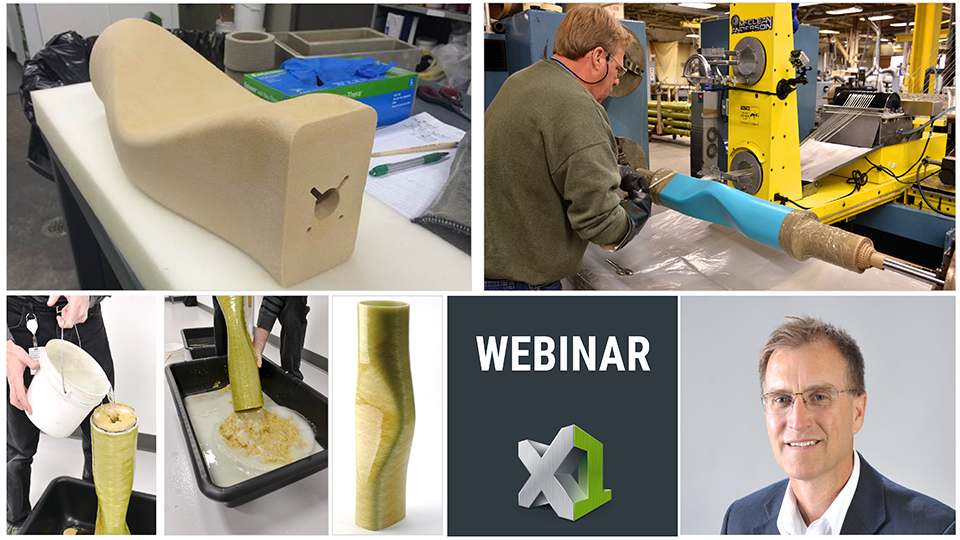
ON-DEMAND WEBINAR: How to 3D Print Sustainable Sacrificial Tooling for Composite Part Production
With today's focus on lightweighting, hollow parts made with composites, such as ducting, fuel tanks, mandrels, and rocket shrouds, are in higher demand than ever before.
View the Webinar.png)
3D Printing Delivers Washout Tooling for Composites
3D Printed washout tooling - an all-new form of sacrificial tooling, is is now being used successfully to create carbon- and glass-fiber reinforced composites for aerospace and defense.
.jpg)
ExOne Presents New S-Max Pro™ Industrial 3D Printer
ExOne Presents New S-Max Pro™ Industrial 3D Sand Printer at the 2019 GIFA Fair
Select Filters Cancel
Applications
Select All
Industries
Select All
News & Events
Select All
Resources
Select All
Systems
Select All
Technology
Select All