- Home
- Binder Jetting Resources
- Blog
Keeping Foundries Flowing
Keeping Foundries Flowing
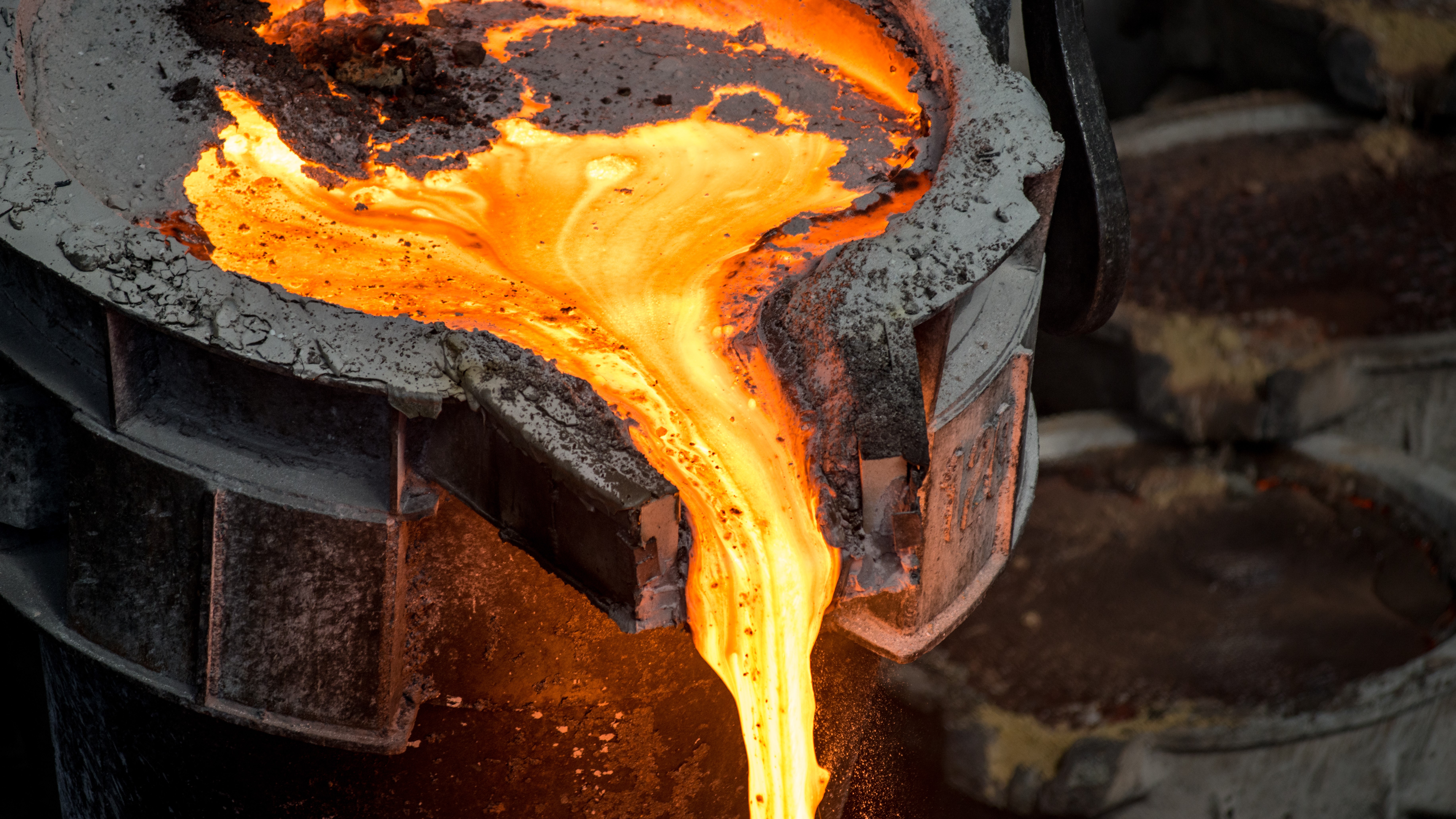
Keeping Foundries Flowing
Sand 3D printing helps foundries build resilient supply chains with flexible core and mold production, without the cost of producing or storing traditional tooling
In our globalized society, making products half a world away from the point of need has become the norm. But the strategic risks with locating manufacturing capacity far away from consumers are increasingly exposed as complex global supply chains struggle to keep materials flowing into and products out of centralized industrial centers. A pandemic, extreme weather events, territorial invasions, and even ill-navigated container ships have clogged manufacturing arteries around the world and forced companies to reevaluate “just-in-time” production strategies.
Increasingly manufacturers are turning to 3D printing as a solution. AM 2.0 technologies like high-speed, high-capacity binder jet 3D printing bring the factory floor closer to consumers. Additive manufacturing enables fast product launches to match rapidly shifting consumer demands and helps reshape the supply chain in favor of locating inventory, or on-demand production capacity, closer to customers.
Flexible and On-Demand Production with Foundry 3D Printing
Foundry 3D printers enable decentralized manufacturing by printing straight from CAD files. Casting without the need for traditional patterns or core boxes means parts are delivered faster. Foundries are using 3D printing to produce molds and cores in under 24 hours and expand business with quick-turn castings without the high cost of investing in hard tooling.
While rapid casting is often touted for prototyping and fast iterations, it is also gaining importance for on-demand spare parts. Sectors like oil and gas value uptime as part of holistic view of parts replacement and the cost of making a spare part is secondary to the economic loss of downtime. However, patterns for castings are often unavailable for equipment first produced decades ago.
Combined with other advanced manufacturing techniques like 3D scanning, binder jetting enables on-demand, local castings of these legacy spare parts without traditional tooling and the long lead time and high investment costs that come with it. Foundries are using 3D printing to quickly produce parts when and where they’re needed and shift the paradigm of what’s possible for replacement parts.
Digital Inventory
Supporting customers ongoing production needs, foundries store traditional tooling in large warehouses, sometimes for decades. The cost to keep customers happy by storing these wood or metal patterns and core boxes may go unnoticed, but factor into a foundry’s overall business costs. Physical inventory also carries the risk of loss from weather events or building damage and wasted labor searching for misplaced core boxes or repairing old patterns.
The digital workflow of additive manufacturing means tooling storage moves out of the warehouse and into the cloud. Foundries can store mold and core CAD files on secure networks enabling digital redundancy without the overhead of physical storage or the need to repair damaged tooling.
A More Sustainable Supply Chain
More responsive production also makes for more sustainable production.
As companies consider the risk of how far critical components must travel, shortened supply chains enabled by additive manufacturing mean fewer trucks on the road and ships in the ocean, significantly reducing emissions and helping mitigate rising fuel prices from further affecting the supply chain. Emission-reduction is also aided by the design freedom of 3D printing that enables new, lightweight and space-saving designs.
Tooling-less casting with sand 3D printing also makes short-run casting economically viable, bringing manufacturing volumes more in-line with demand. This helps eliminate the waste of inflated production numbers used to justify the high cost of traditional tooling.
The Next Era of Metalcasting
3D printing helps manufacturers create more resilient supply chains by enabling flexible, local, and tooling-less production. Foundries looking to meet rapidly shifting demands and operate efficiently with less labor are finding a solution with sand 3D printing. Binder jetting helps optimize business to deliver castings with complex designs and fast turnarounds, while saving money on patterns, molds, and labor.
Get Started with Foundry 3D Printing Today
Use us for on-demand core and mold production with engineering support or let's talk about bringing additive manufacturing in-house at your foundry
contact us