- Home
- Binder Jetting Ressources
- Neuigkeiten
ExOne Expert: Ishan Thakore
ExOne Expert: Ishan Thakore
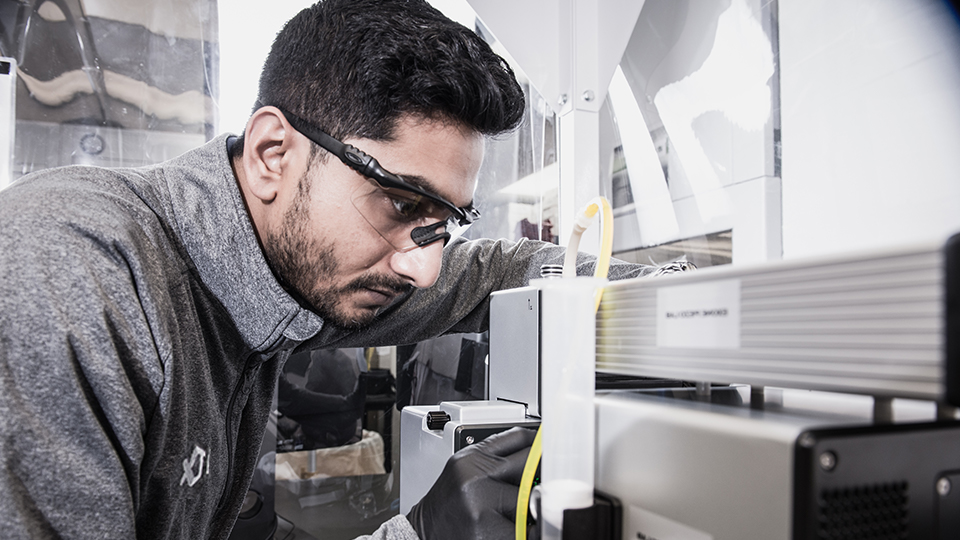
ExOne Expert: Ishan Thakore
Our resident printhead engineer is an active maker space developer using his piezo technology expertise to build an unparalleled printhead lab
Finding the perfect fusion between hobby and career, ExOne Printhead Engineer Ishan Thakore has worked with Fuji printheads for over a decade and specializes in piezo technology, aligning with the premium piezoelectric printheads found in ExOne binder jetting systems.
Already experienced working with two axes in the textile and graphics industry, Thakore jumped at the opportunity to join the ExOne team, noting the symmetry in his experience and getting to work with the binder jetting leaders to advance additive manufacturing technology. “It’s a perfect fit,” he said. “Using piezo printheads for visually printing on textiles is what I've specialized in previously, so I was really familiar with the technology; what a printhead is, how to design a control board, how to integrate these systems with a PLC drive and a servo motor, and how to make it all functional. So, for me to catch on adding another axis was more like, oh, this is a moving train but I'm already at 80 miles per hour.”
As a mechanical engineer who has built his own maker spaces and worked with students to encourage innovative mentorship, he highlights the need for systematic processes to advance binder jetting. As ExOne systems are increasingly installed for serial production applications, his goal is to make the printhead operate efficiently, reliably, and with a degree of confidence that comes with established, scientific, and certified processes.
There are a lot of factors when you’re building a printhead and when you’re working with sub-micron sizes you want to eliminate anything that could be a causality for contamination, so a class 100 clean room is necessary.
Ishan Thakore
Printhead engineer
Sitting in his home-based maker space office, Thakore shows off his latest project, a six degrees of freedom (6DoF) e-chain 3D printer with an integrated active bed monitoring system. He’s built in a temperature and humidity sensor that moves with the printhead so he can actively monitor whether prints are going to warp in the future.
Since his early days as a maker, he fully embraced the fail fast philosophy. “I wanted my creativity to be free to experiment. I don't care if I blow it up, but I'll learn. And that’s part of it, you know? That's the beauty of it.” He carries this spark of creativity into his career where he is tasked with building a state-of-the-art lab to improve the understanding of printhead technology while establishing best practices that help educate customers. “We want to achieve printhead accuracy and not compromise,” he said.
Understanding firsthand the challenges of volume production with industrial printheads, he’s aiming to take a scientific approach to develop the art of binder dispensing and further optimize ExOne technology.
For example, over the past two decades drops were evaluated by mass measurement that never provided the ability to view how the drops are ejected, what their shape is, or what their velocity is. Thakore notes that digital technologies can enable deeper understanding and provide more information to make deliberate optimizations. “We live in a time now where we can use a camera to identify a single drop and AI to recognize its properties, then evaluate it to make informed decisions,” he said.
Emphasizing the importance of consistency alongside precision,
Thakore explained the systematic approach of ExOne in analyzing the binder ejection process of printheads using the example of redundant equipment to test and verify information He said, “We have two drop watcher systems by competing suppliers – one at our U.S. headquarters and another at our German facility. With two different systems we expect the same result if we’re working accurately and consistently.”
Because drops ejected from a printhead are measured in picolitres, one trillionth of a liter or 10 to the 12th power, Thakore required the printhead lab to be a clean room that could ensure the integrity of the workspace. “There are a lot of factors when you’re building a printhead and when you’re working with sub-micron sizes you want to eliminate anything that could be a causality for contamination, so a Class 100 clean room is necessary,” he explained. Class 100 clean rooms are certified laboratories with controlled levels of airborne particles and parameters such as humidity and temperature. ExOne's Class 100 clean room includes a dedicated, sealed HVAC system, ionized air shower entry, and laminar flow hood. Laser alignment equipment ensures the positional accuracy of printheads while drop watcher high-speed cameras identify and analyze drop properties with artificial intelligence.
With a lab able to study binder drops to sub-micron accuracy, he aims to expand the fundamental knowledge of binder jetting and contribute to its maturity by leading the way in printhead innovation. “I'm not talking about band-aids, I want us to be on the forefront and want the industry to say, ‘we want a lab like ExOne,’” he concluded.