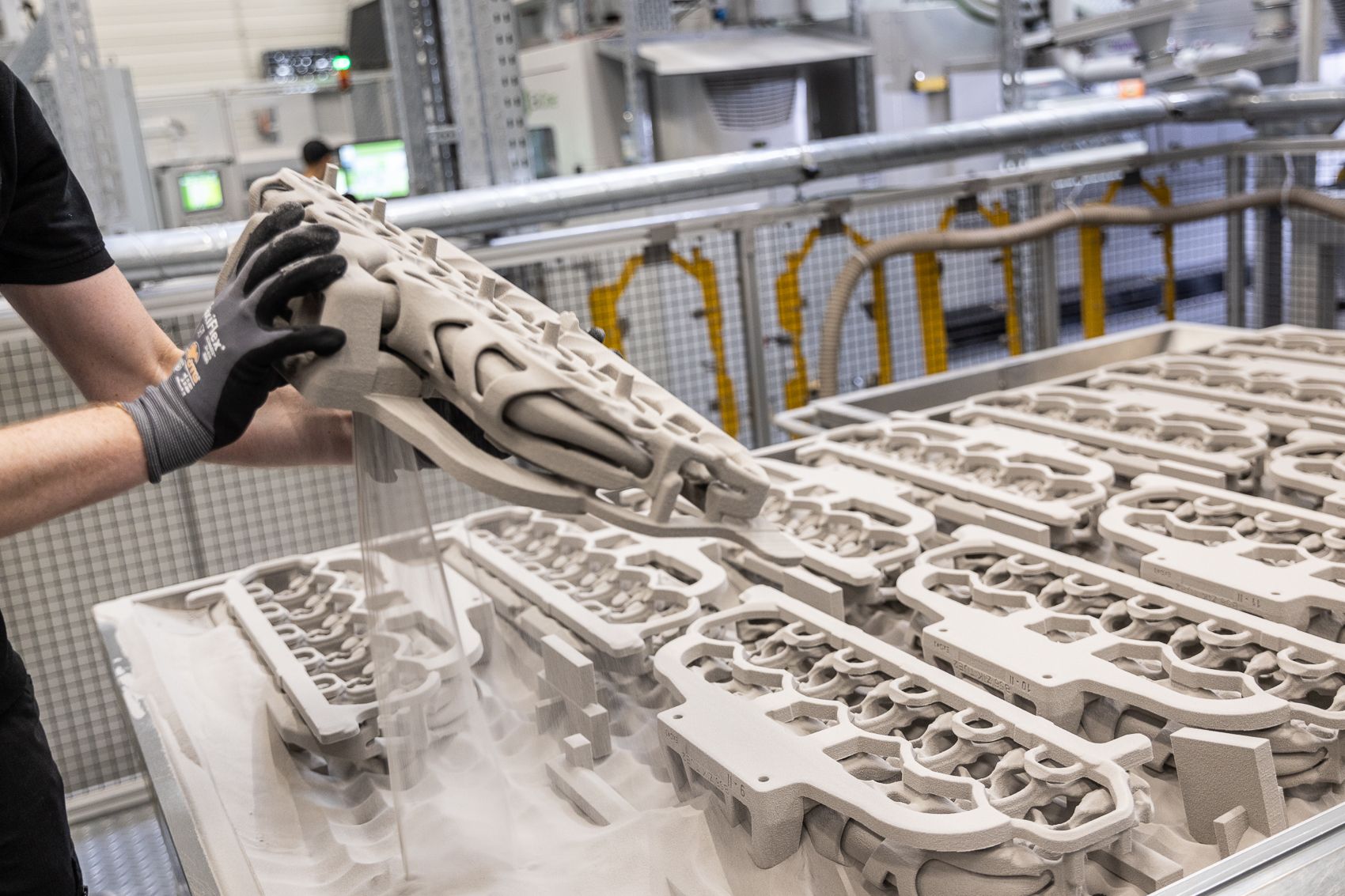
Inside the Pioneering Additive Manufacturing Journey of BMW and ExOne
Learn how ExOne’s binder jet 3D printing technology helps BMW make its sustainable manufacturing vision a reality in serial production.
Learn More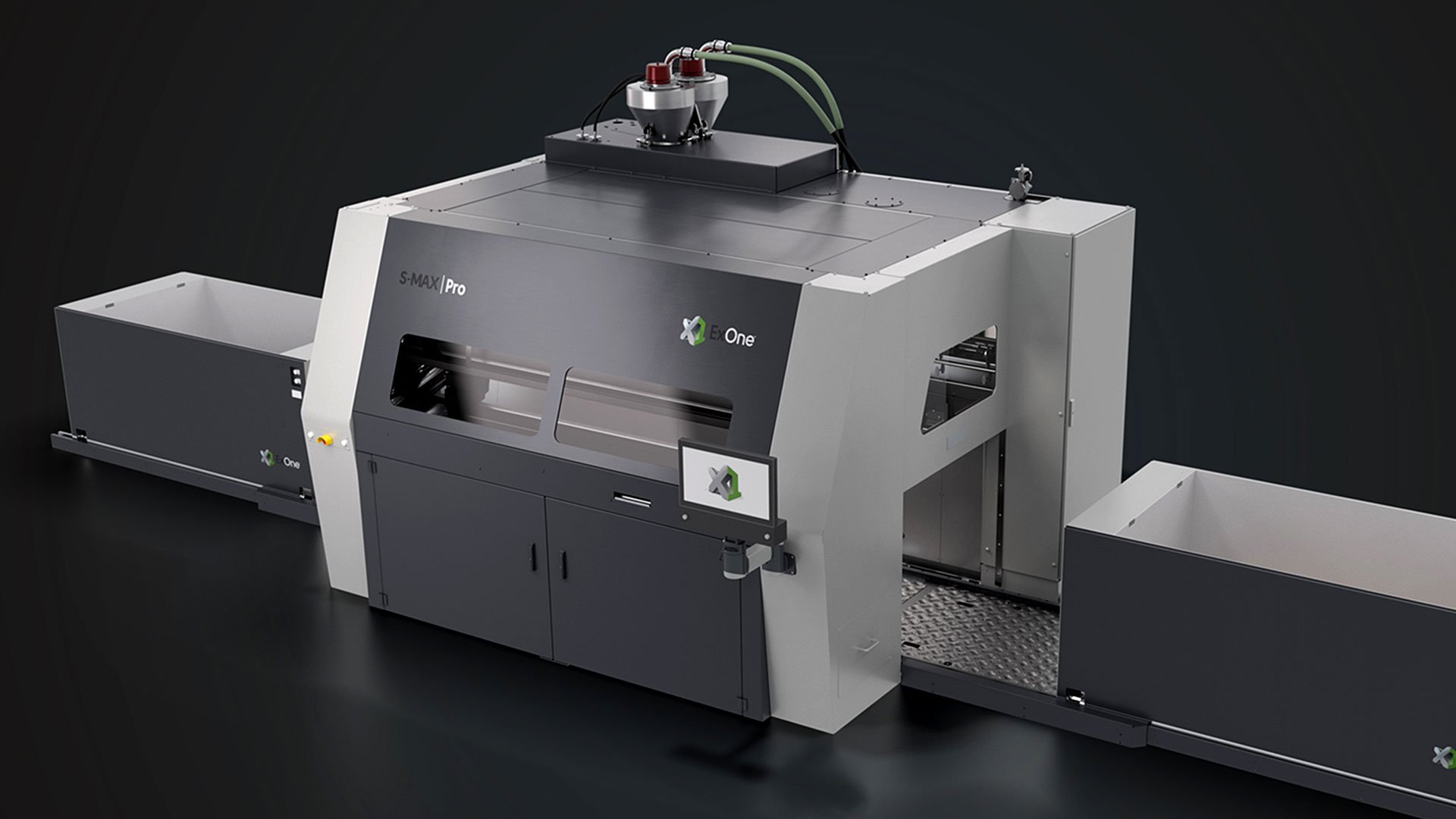
S-Max® Pro Production Sand 3D Printer
The S-Max® Pro delivers an industry-leading combination of speed and precision on a system that can process all ExOne binder systems for reliable production of complex cores and molds. Foundries are able to do more with integrated automation that enables lights-out manufacturing.
Learn More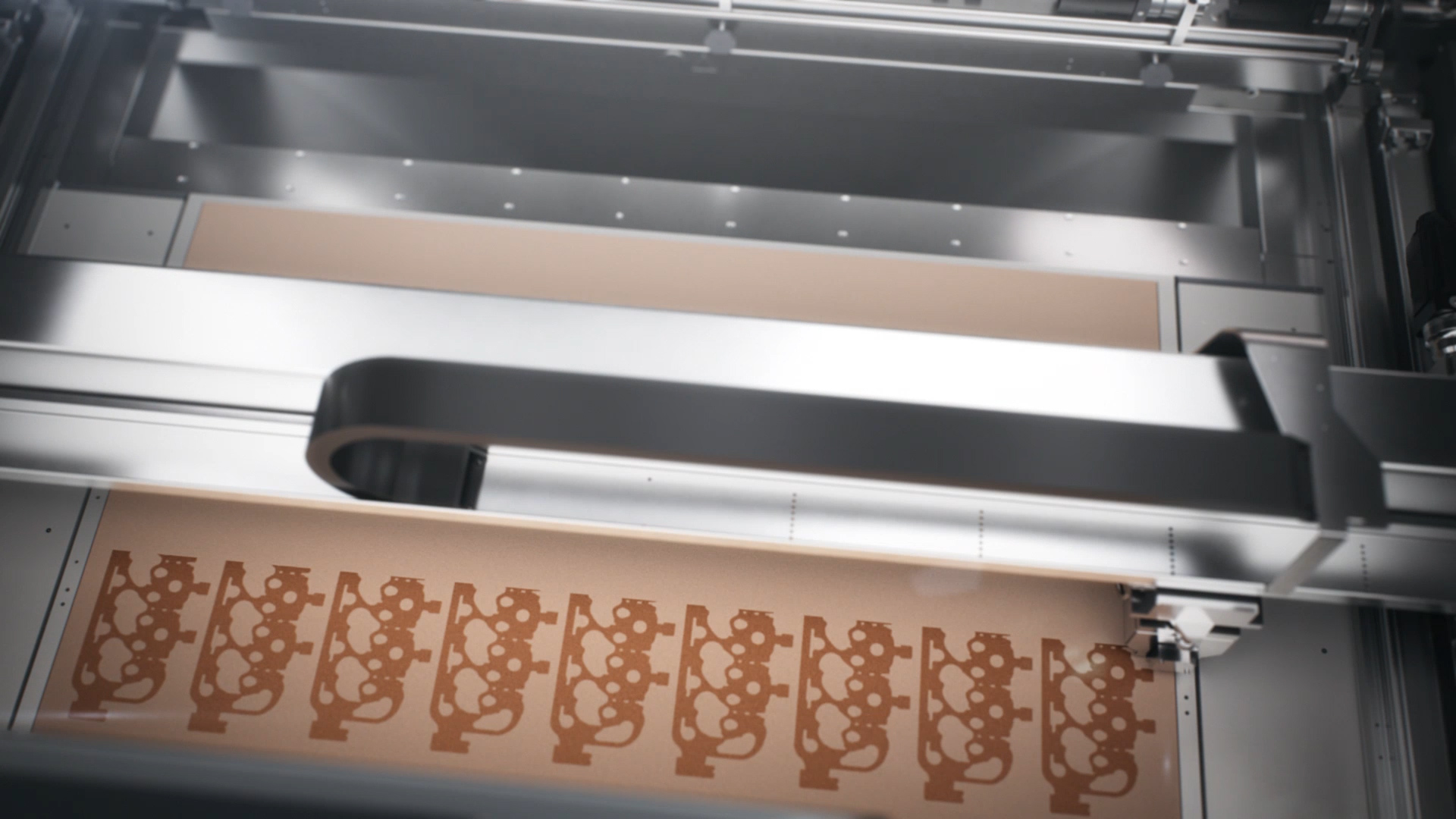
Binder Jet 3D Printing
ExOne industrial binder jet 3D printers enable a digital workflow to deliver complex designs with fast turnarounds for a range of applications from metalcasting molds and cores to rapid tooling.
Binder Jet 101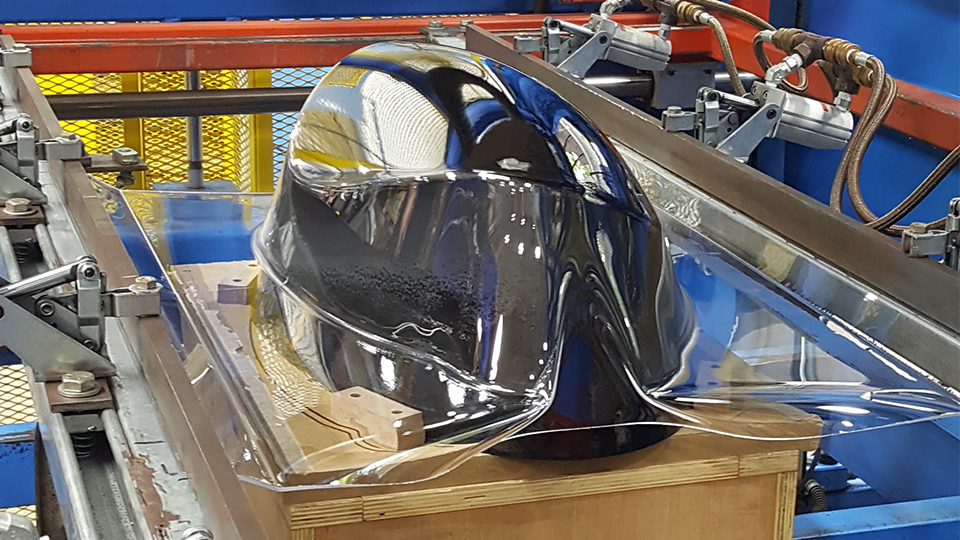
Fast, affordable tooling for the final production of metal, plastic, and composite designs
X1 Tooling 3D printed tools for plastic injection molding, thermoforming, composite layup, sacrificial tooling, and metalcasting. Get complex final parts in days versus weeks and months.
Learn More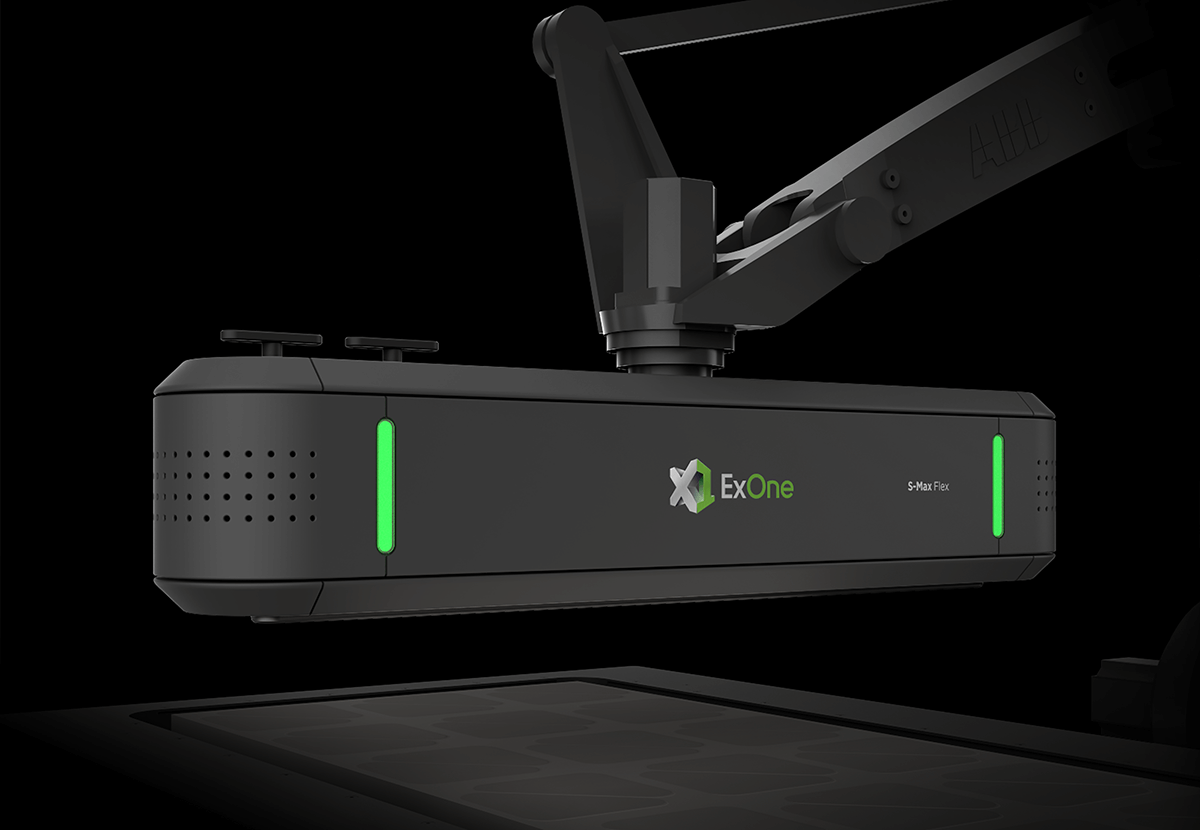
Introducing the S-Max® Flex
The all-new S-Max Flex robotic sand 3D printer debuts April 23 at CastExpo in Columbus, OH. The affordable system was developed to make 3D printing accessible to every foundry, helping metalcasting businesses survive and thrive into the future. Take a peek at the S-Max Flex now and learn how sand 3D printing can help you operate more efficiently
S-Max® Flex System DetailDigital Metalcasting Experts, Foundry Partners
As a leader in additive manufacturing for over two decades, ExOne sand 3D printers have helped foundries and pattern shops transform sandcasting by eliminating the need for hard tooling. Our binder jet 3D printing technology enables digital foundries to produce previously impossible shapes, consolidate complex cores to reduce assembly, or iterate design changes without the time or investment of traditional tooling.
With a team of 3D printing and foundry experts, ExOne is committed to your success with binder jetting. Our team provides full systems and support, engineering services and casting simulation for high-value done-in-one pours, and on-demand 3D printing of complex molds and cores as well as infiltrated sand tooling for a variety of applications.
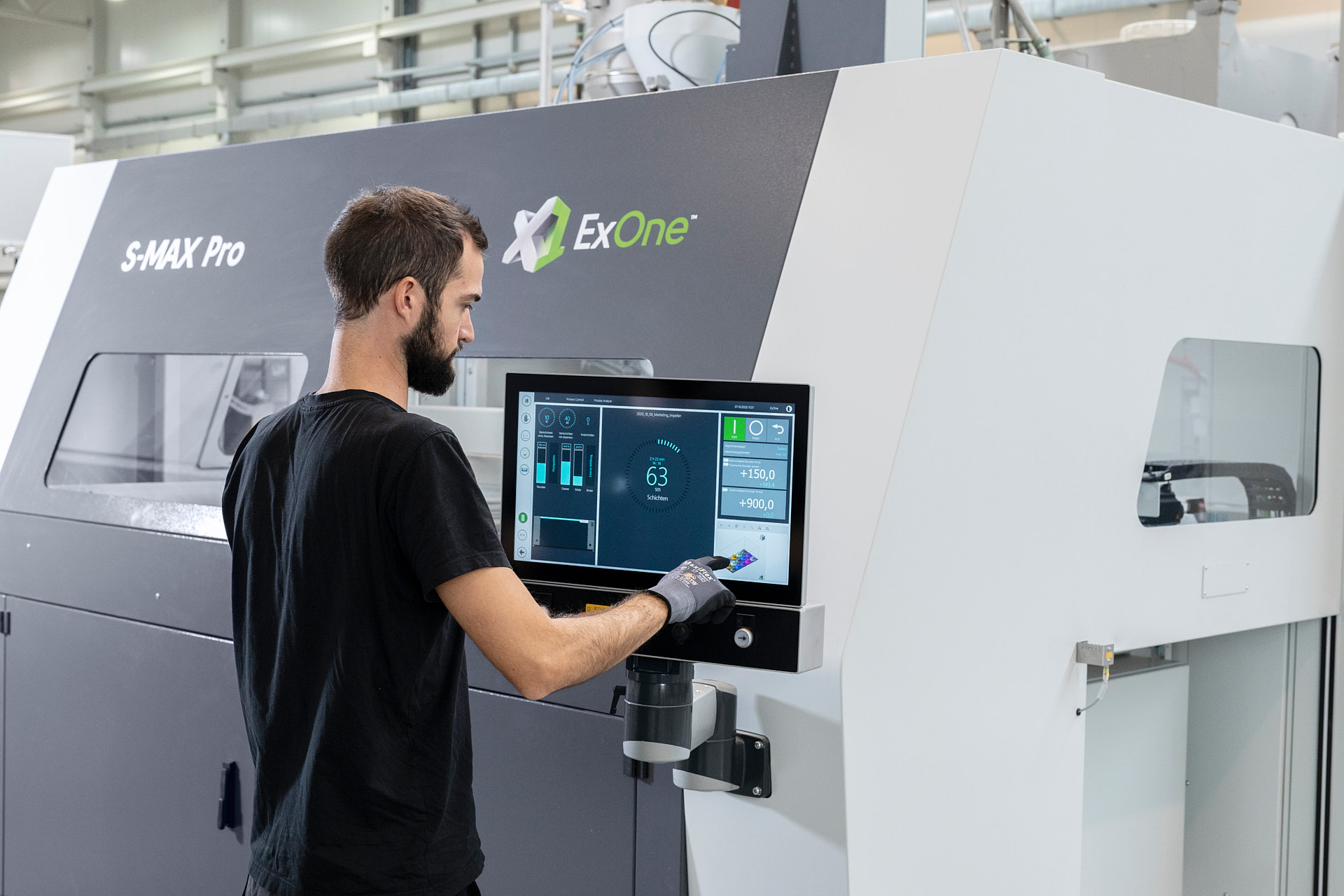
Sand 3D Printers
Foundry 3D printers from ExOne support sandcasting applications with enhanced designs and fast turnaround times. With a variety of systems to meet every production requirement and price, our binder jetting machines produce complex cores and molds without the cost and lead times of traditional tooling.
Foundry 3D Printing Systems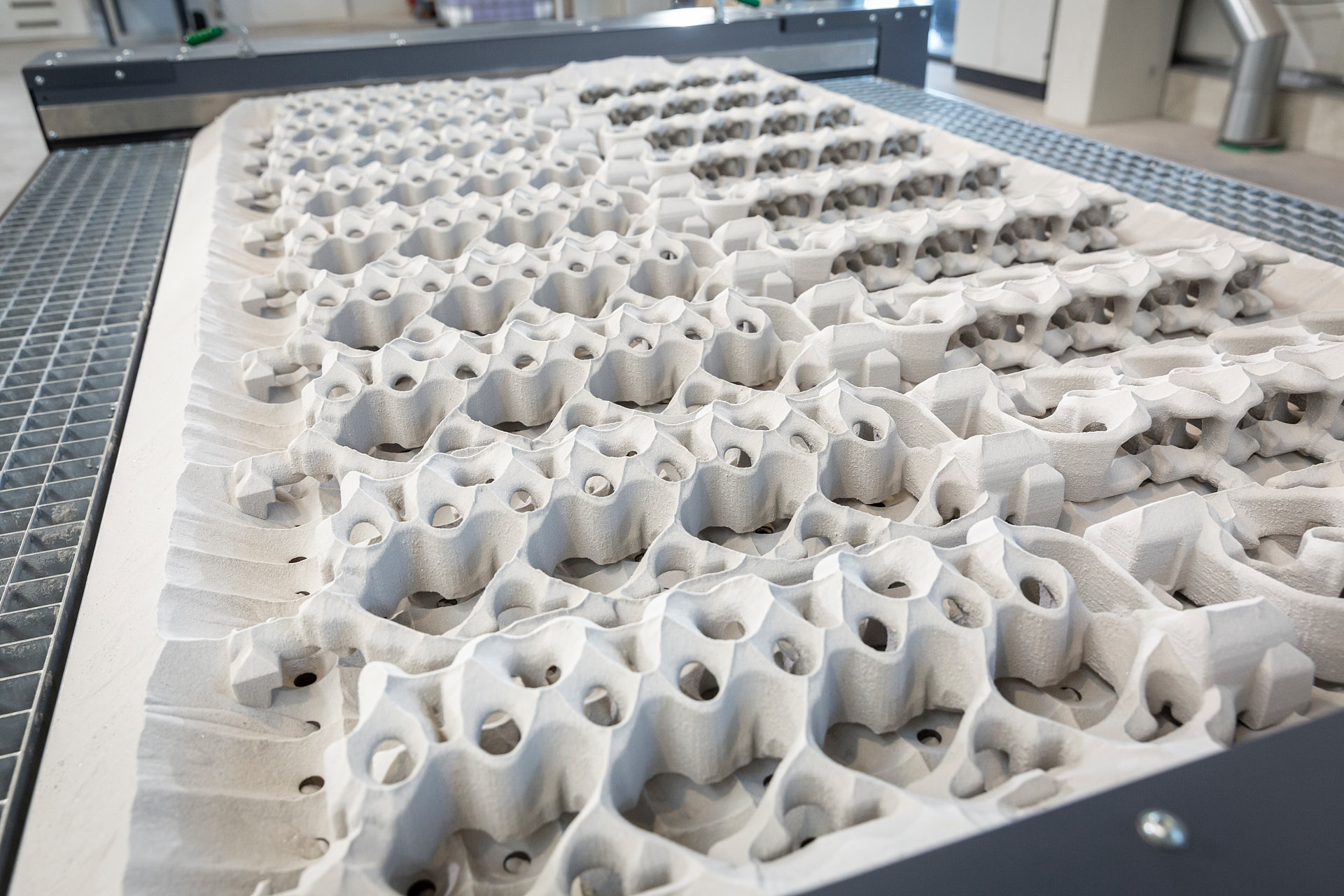
Materials & Binders
The leaders in 3D sandcasting, ExOne offers a variety of sand and binder combinations for both ferrous and nonferrous processes. From high-strength casting media to emission-free, defect-free inorganic binder, we tailor 3D printing with sand to your foundry’s needs.
Material Flexibility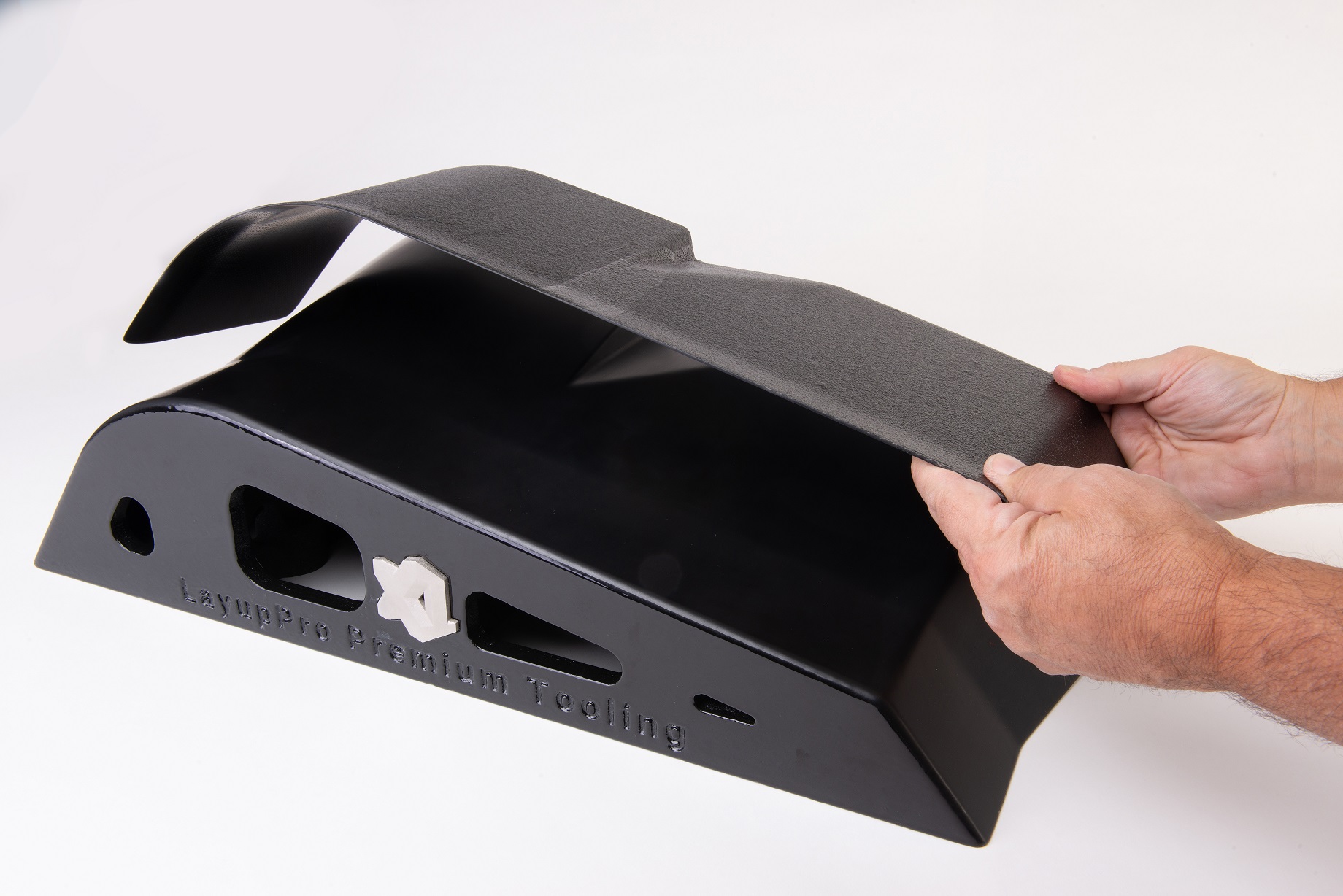
X1 Tooling
ExOne offers solutions for metal, plastic, composite, and foam part production with on-demand tooling solutions. Create unique geometries, iterate quickly, and test functional prototypes to improve products while getting to market faster and cheaper.
Rapid Tooling SolutionsKimura Foundry America
After all of our research on all of the 3D printer vendors in the world, we determined that ExOne printers are better and they have a very high-end technology, and very good print quality.
Dr. Yoya Fukuda, Ph.D.